Aircraft structural part cutting parameter optimization method based on characteristics
A technology for aircraft structural parts and cutting parameters, which is applied in special data processing applications, electrical digital data processing, instruments, etc., can solve problems such as poor versatility, easy deformation in processing, and easy occurrence of snap knives at corners. The effect of suppressing chatter vibration and improving machining efficiency
- Summary
- Abstract
- Description
- Claims
- Application Information
AI Technical Summary
Problems solved by technology
Method used
Image
Examples
Embodiment Construction
[0028] The following structural drawings and embodiments further illustrate the present invention.
[0029] Such as Figure 1-4 shown.
[0030] figure 1 It is a flow chart of the feature-based cutting parameter optimization method for aircraft structural parts of the present invention. Such as figure 1 As shown, the feature-based cutting parameter optimization method of aircraft structural parts of the present invention comprises the following steps:
[0031] 1. Extract the influencing factors of feature rigidity.
[0032] Such as figure 2 The features of the parts shown mainly include groove web, groove inner shape, rib feature, outline feature, corner feature and hole feature. Through identification, the size parameters of web feature, rib feature, inner shape feature and outline feature can be obtained, while the corner Features and hole features are usually considered in the web and inner shape features;
[0033] 2. Cutting force prediction.
[0034] According to ...
PUM
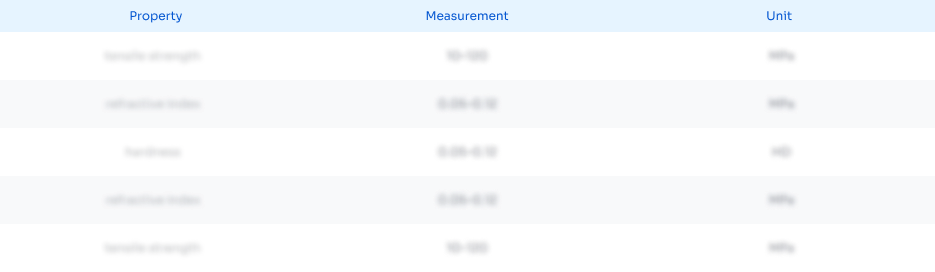
Abstract
Description
Claims
Application Information

- R&D Engineer
- R&D Manager
- IP Professional
- Industry Leading Data Capabilities
- Powerful AI technology
- Patent DNA Extraction
Browse by: Latest US Patents, China's latest patents, Technical Efficacy Thesaurus, Application Domain, Technology Topic, Popular Technical Reports.
© 2024 PatSnap. All rights reserved.Legal|Privacy policy|Modern Slavery Act Transparency Statement|Sitemap|About US| Contact US: help@patsnap.com