Gasified coal-water-slurry preparation process and corresponding production line
A technology for gasification of coal-water slurry and preparation process, which is applied in the gasification of granular/powdered fuel, petroleum industry, liquid carbon-containing fuel, etc. Long-term stable operation and other problems, to achieve the effect of reasonable particle size distribution of coal slurry, improved throughput capacity, and increased load
- Summary
- Abstract
- Description
- Claims
- Application Information
AI Technical Summary
Problems solved by technology
Method used
Image
Examples
Embodiment 1
[0029] Embodiment one: if figure 1 As shown, the special-purpose production line of the preparation new technology of gasification coal-water slurry of the present invention comprises coal storage bunker 1, coal mill 2 and fine mill 3, and wherein coal storage bunker 1 feeding port is provided with a weighing feeder 4, The measured coal enters the drum feeder 5, mixes with additives and water according to the proportion, and then enters the coal mill 2 for grinding, and the ground coal water slurry passes through the coal mill outlet chute 6 and the low-pressure coal slurry pump 7. The degasification furnace 8 is characterized in that: a circuit pump 9 is also connected to the discharge trough 6 of the coal mill, and the outlet of the circuit pump 9 is connected to a coarse slurry rotary vibrating screen 10, and the coarse slurry rotary vibrating screen 10 Water inlet pipe 11 and additive feeding pipe 12 are also provided on the top, the oversize of this coarse slurry rotary v...
Embodiment 2
[0035] Such as figure 2 Shown: embodiment two: this gasification coal-water slurry preparation process comprises following operation:
[0036]1). Coal, water and additives are processed into coal water slurry by coal mill 2, wherein the weight mixing ratio of coal, water and additives is 65:28:1;
[0037] 2). The coal-water slurry obtained in process 1) is divided into two paths, one path of coal-water slurry is directly sent to gasifier 8, and the path of coal-water slurry accounts for 80% of the output of coal mill 2; the other path of coal-water slurry is mixed with water and After additive, send into a coarse slurry rotary vibrating screen 10;
[0038] After the coarse slurry rotary vibrating screen 10 screens out large particles, the remaining coal-water slurry is sent to the fine mill 3, and after the fine mill 3 grinds, the coal-water slurry is mixed with flushing water again at the slurry outlet 15 of the fine mill, and finally forms Fine coal slurry with a concentr...
Embodiment 3
[0041] Embodiment three: the gasification coal-water slurry preparation process comprises the following procedures:
[0042] 1).Use the coal mill 2 to process coal, water and additives into coal water slurry, wherein the weight mixing ratio of coal, water and additives is 60:30:1
[0043] 2). The coal-water slurry obtained in process 1) is divided into two paths, one path of coal-water slurry is directly sent to the gasifier 8, and the path of coal-water slurry accounts for 90% of the output of coal mill 2; the other path of coal-water slurry is mixed with water and After additive, send into a coarse slurry rotary vibrating screen 10;
[0044] After the coarse slurry rotary vibrating screen 10 screens out large particles, the remaining coal-water slurry is sent to the fine mill 3, and after the fine mill 3 grinds, the coal-water slurry is mixed with flushing water again at the slurry outlet 15 of the fine mill, and finally forms The concentration is 47% fine coal slurry;
[...
PUM
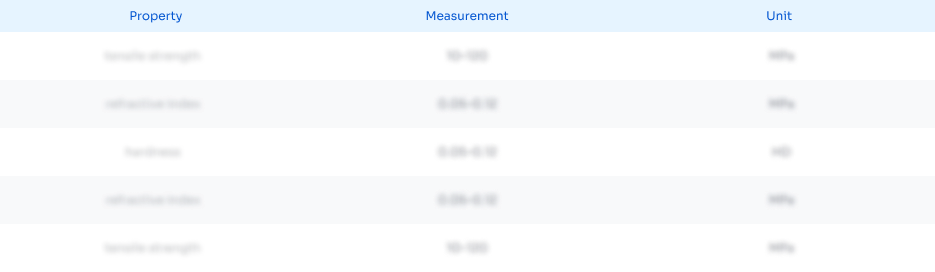
Abstract
Description
Claims
Application Information

- R&D
- Intellectual Property
- Life Sciences
- Materials
- Tech Scout
- Unparalleled Data Quality
- Higher Quality Content
- 60% Fewer Hallucinations
Browse by: Latest US Patents, China's latest patents, Technical Efficacy Thesaurus, Application Domain, Technology Topic, Popular Technical Reports.
© 2025 PatSnap. All rights reserved.Legal|Privacy policy|Modern Slavery Act Transparency Statement|Sitemap|About US| Contact US: help@patsnap.com