Method for lowering contents of oxygen and nitrogen in molten steel at smelting end in semisteel smelting converter
A technology for steelmaking converter and nitrogen content, applied in the field of nitrogen content and control of molten steel oxygen at the smelting end point of semi-steel steelmaking converter, can solve the problems of increasing nitrogen in molten steel, reducing the oxygen activity of molten steel at the end point, affecting the quality of molten steel, etc., and reaching the end point The effect of low total iron content in slag, reduction of oxygen and nitrogen content, and reduction of erosion
- Summary
- Abstract
- Description
- Claims
- Application Information
AI Technical Summary
Problems solved by technology
Method used
Examples
example 1
[0025] A steel plant mixed semi-steel after vanadium extraction into a 200t converter for smelting. The carbon content of the semi-steel into the furnace was 3.5% and the temperature was 1274°C. In order to avoid deep blowing or high temperature caused by low temperature in the furnace, no scrap steel is added after adding semi-steel and smelting starts. Before the amount of oxygen blown in semi-steel smelting reaches 75% of the total amount of oxygen blown in the entire semi-steel smelting process, carbon dioxide is blown at the bottom, and the gas supply intensity is 0.03m 3 / (min t 钢 ), the position of the oxygen lance is controlled at 1.8~2.0m; when the amount of oxygen blown in semi-steel smelting reaches 75~90% of the total amount of oxygen blown in the whole semi-steel smelting process, the position of the oxygen lance is reduced to 1.2~ 1.4m, bottom blowing argon, gas supply intensity is 0.02m 3 / (min t 钢 ); when the amount of oxygen blown in semi-steel smelting rea...
example 2
[0028] A steel factory mixed semi-steel after vanadium extraction into a 120t converter for smelting. The carbon content of the semi-steel into the furnace was 3.7% and the temperature was 1274°C. In order to avoid deep blowing or high temperature due to low temperature in the furnace, add 17.8kg / t after adding semi-steel 钢 Scrap steel and start smelting. Before the amount of oxygen blown in semi-steel smelting reaches 75% of the total amount of oxygen blown in the entire semi-steel smelting process, carbon dioxide is blown at the bottom, and the gas supply intensity is 0.04m 3 / (min t 钢 ), the position of the oxygen lance is controlled to be 2.2-2.5m; when the amount of oxygen blown in semi-steel smelting reaches 75-90% of the total amount of oxygen blown in the whole process of semi-steel smelting, reduce the position of the oxygen lance to 1-2.5m 1.2m, bottom blowing argon, gas supply intensity is 0.03m 3 / (min t 钢 ); when the amount of oxygen blown in semi-steel smelti...
example 3
[0031] A steel plant mixed semi-steel after vanadium extraction into an 80t converter for smelting. The carbon content of the semi-steel into the furnace was 3.5% and the temperature was 1294°C. In order to avoid deep blowing or high temperature due to low temperature in the furnace, add 13.6kg / t after adding semi-steel 钢 Scrap steel and start smelting. Before the amount of oxygen blown in semi-steel smelting reaches 75% of the total amount of oxygen blown in the entire semi-steel smelting process, carbon dioxide is blown at the bottom, and the gas supply intensity is 0.05m 3 / (min t 钢 ), the position of the oxygen lance is controlled at 2-2.4m; when the amount of oxygen blown in the semi-steel smelting reaches 75-90% of the total amount of oxygen blown in the whole semi-steel smelting process, the position of the oxygen lance is reduced to 1.1- 1.3m, bottom blowing argon, gas supply intensity is 0.04m 3 / (min t 钢 ); when the amount of oxygen blown in semi-steel smelting r...
PUM
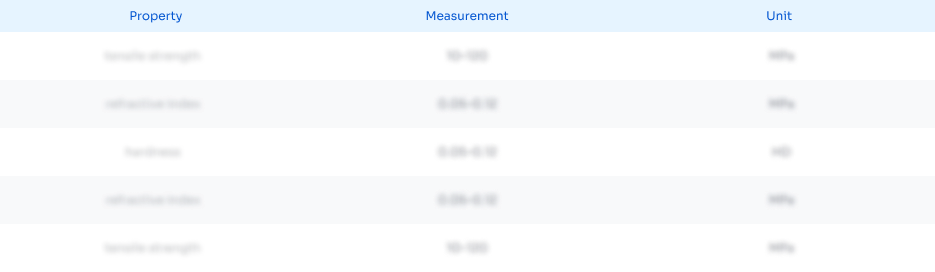
Abstract
Description
Claims
Application Information

- R&D
- Intellectual Property
- Life Sciences
- Materials
- Tech Scout
- Unparalleled Data Quality
- Higher Quality Content
- 60% Fewer Hallucinations
Browse by: Latest US Patents, China's latest patents, Technical Efficacy Thesaurus, Application Domain, Technology Topic, Popular Technical Reports.
© 2025 PatSnap. All rights reserved.Legal|Privacy policy|Modern Slavery Act Transparency Statement|Sitemap|About US| Contact US: help@patsnap.com