Process for heating sleeve shaft through magnetic induction by large ring component
A technology of electromagnetic induction heating and process method, which is used in metal processing, metal processing equipment, manufacturing tools, etc.
Inactive Publication Date: 2013-06-26
HARBIN ELECTRIC MASCH CO LTD
View PDF2 Cites 9 Cited by
- Summary
- Abstract
- Description
- Claims
- Application Information
AI Technical Summary
Problems solved by technology
However, it is not suitable for thermal sleeve of components that cannot be heated by peripheral magnetic induction, such as radial rotor brackets with rotor arms.
Method used
the structure of the environmentally friendly knitted fabric provided by the present invention; figure 2 Flow chart of the yarn wrapping machine for environmentally friendly knitted fabrics and storage devices; image 3 Is the parameter map of the yarn covering machine
View moreExamples
Experimental program
Comparison scheme
Effect test
Embodiment Construction
[0008] Equipment required:
[0009] ●One intermediate frequency welding machine
[0010] ●Sufficient length of electromagnetic induction line
[0011] ●One outside micrometer
[0012] ●One set of 300mm inner diameter micrometer
[0013] ●A inner diameter measuring rod
[0014] ●Open end wrench for fixed shaft
[0015] ●0.3mm steel wire 10m
[0016] ●Piano wire headphone battery set
[0017] ●A thermometer.
the structure of the environmentally friendly knitted fabric provided by the present invention; figure 2 Flow chart of the yarn wrapping machine for environmentally friendly knitted fabrics and storage devices; image 3 Is the parameter map of the yarn covering machine
Login to View More PUM
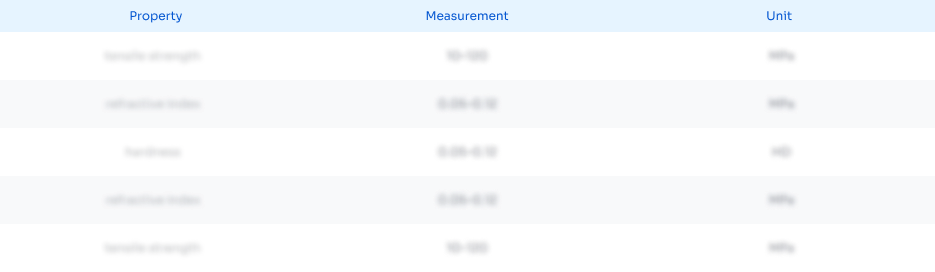
Abstract
The invention relates to a process for heating a sleeve through magnetic induction by a large ring component. Finish machining is conducted on the ring component until certain size of the ring component is reached before shrinkage fit. In order to avoid thermal consumption after heating and prevent the surface of a ring from being burned due to the fact of partial overheat, asbestos cloth is coated and surrounds the outer surface of the ring, induction coils are wound on the outer surface of the ring, the ring is lifted above a rotating shaft through a crane, and after the ring is heated, when the minimum size of the ring is detected to meet requirements of a drawing through a measuring bar, the ring is smoothly dropped, and the shrinkage fit is conducted on the ring. After the ring is cooled to room temperature, size difference of an outer ring of the ring before the shrinkage fit and after the shrinkage fit is not larger than 0.02 millimeter. After the shrinkage fit is finished for the first time, the ring does not need machining a large equipment for the second time again after the shrinkage fit, the lowest heating temperature is controlled through intermediate-frequency electromagnetic induction heating, and deformation of the ring is small after the shrinkage fit after the ring is heated. The process for heating the sleeve shaft through magnetic induction by the large ring component has the advantages of being simple in operation, simple in required equipment, low in manufacturing cost, short in working period and the like, can save a large amount of cost from secondary machining to large-equipment machining, and is very high in application value.
Description
technical field [0001] The invention relates to a process method for heating a sleeve shaft of a large circular ring component by magnetic induction. Background technique [0002] Sliding rotors and hub-type rotor brackets with fixed stator shafts for large hydro-generators generally adopt tight fits to transmit torque. In the past, the process method is to heat a single piece after rough machining and heat it up. This conventional method is difficult to control the temperature, most of which are above 300 degrees. Due to the high temperature during the heat sleeve, the shrinkage of the root of the shaft shoulder is relatively large during cooling and contraction, resulting in a large gap, which is unfavorable to the overall performance of the unit. Moreover, it takes too long to adjust and transport after heating, and the heat loss is serious. It is easy to get stuck during the heat-fitting process, and the heat-fitting requirements cannot be fulfilled. After the thermal ...
Claims
the structure of the environmentally friendly knitted fabric provided by the present invention; figure 2 Flow chart of the yarn wrapping machine for environmentally friendly knitted fabrics and storage devices; image 3 Is the parameter map of the yarn covering machine
Login to View More Application Information
Patent Timeline

Patent Type & Authority Applications(China)
IPC IPC(8): B23P11/02
Inventor 于久清
Owner HARBIN ELECTRIC MASCH CO LTD
Features
- R&D
- Intellectual Property
- Life Sciences
- Materials
- Tech Scout
Why Patsnap Eureka
- Unparalleled Data Quality
- Higher Quality Content
- 60% Fewer Hallucinations
Social media
Patsnap Eureka Blog
Learn More Browse by: Latest US Patents, China's latest patents, Technical Efficacy Thesaurus, Application Domain, Technology Topic, Popular Technical Reports.
© 2025 PatSnap. All rights reserved.Legal|Privacy policy|Modern Slavery Act Transparency Statement|Sitemap|About US| Contact US: help@patsnap.com