Best strain of austenitic stainless steel container welding residual stress overload reducing method
A technology of austenitic stainless steel and residual stress, applied in the direction of improving process efficiency, etc., can solve the problem of not doing the best strain, and achieve the effect of reliability assurance
- Summary
- Abstract
- Description
- Claims
- Application Information
AI Technical Summary
Problems solved by technology
Method used
Image
Examples
example 1
[0039] Such as figure 1 As shown, in Embodiment 1 of the present invention, a circular pressure vessel made of austenitic stainless steel is used. The circular pressure vessel has an inner diameter of 600 mm and a wall thickness of 5 mm, including an oval head 1, a barrel section 2, and a barrel section 3. Cone 4, connecting flange 5, reinforcing ring 6, support 7 and backing plate 8. The components of the circular pressure vessel are mainly composed of three kinds of dissimilar steel materials: 06Cr19Ni10, 022Cr17Ni12Mo2 and Q235B. Among them, the oval head 1, the barrel section 2, the cone 4, the connecting flange 5, the reinforcing ring 6 and the backing plate 8 are respectively It is made of 06Cr19Ni10 dissimilar steel, the barrel section 3 is made of 022Cr17Ni12Mo2 dissimilar steel, and the support 7 is made of Q235B dissimilar steel.
[0040] The cylindrical body of the circular pressure vessel is rolled by a plate rolling machine, the cone is cold rolled by a plate rol...
example 2
[0049] Such as figure 2 and image 3 As shown, in Embodiment 2 of the present invention, a square jacketed container with tie bars is used. The material of the main body of the container is 5mm thick 06Cr19Ni10 and 022Cr17Ni12Mo2 two kinds of dissimilar steels, and the material of the tie bars and the jacket is Q235B steel. Plug welding is used between the jacket and the tie bars, and symmetrical intermittent fillet welds are used between the main body and the tie bars. Stress corrosion occurs in this fillet weld in a short period of time during use. The purpose of the treatment is to reduce the main body of the fillet weld area. welding residual stress.
[0050] The square jacketed container with tie bars includes a main body plate 13, a main body plate 14, a sealing plate 15, a jacket plate 16, a tie bar 17, and a pipe joint 18, wherein the main body plate 13 and the sealing plate 15 are made of 06Cr19Ni10 material, The main body plate 14 is made of 022Cr17Ni12Mo2 materia...
PUM
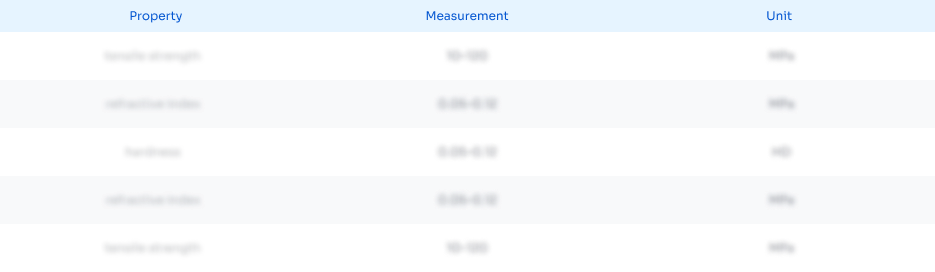
Abstract
Description
Claims
Application Information

- R&D Engineer
- R&D Manager
- IP Professional
- Industry Leading Data Capabilities
- Powerful AI technology
- Patent DNA Extraction
Browse by: Latest US Patents, China's latest patents, Technical Efficacy Thesaurus, Application Domain, Technology Topic, Popular Technical Reports.
© 2024 PatSnap. All rights reserved.Legal|Privacy policy|Modern Slavery Act Transparency Statement|Sitemap|About US| Contact US: help@patsnap.com