Two-flow tube header structure of wound-tube-type heat exchanger
A heat exchanger, dual-process technology, applied in the direction of heat exchanger shell, heat exchange equipment, lighting and heating equipment, etc., can solve the problems of inconvenient maintenance and operation of equipment, complicated shell side structure, excessive opening and reinforcement, etc. Design calculation and manufacturing difficulty, reduce manufacturing difficulty and production cost, and facilitate maintenance and repair operations.
- Summary
- Abstract
- Description
- Claims
- Application Information
AI Technical Summary
Problems solved by technology
Method used
Image
Examples
Embodiment 2
[0031] Embodiment 2, on the basis of Embodiment 1, the shape of the tube box included in the tube box structure, the number of supporting ribs and the connection position are optimized, wherein the shapes of the tube section B5-3 and the tube section A4-3 are preferably cylinders shape, it is beneficial to reduce the flow loss of the stream medium entering the pipe box in the pipe box, the integrity is good and it is easy to manufacture, and the rib plate between the head B5-2 and the barrel section B5-3 and the barrel section A4-3 The number of 7 pieces is not less than 3, preferably 3 pieces, and they are evenly arranged along the circumference of the barrel section A4-3 to ensure the stability of the connection structure of the inner and outer pipe boxes.
[0032] In actual production, the drainage design of the pipe box is usually such that the stream with high medium pressure flows through the outer pipe box, while the stream with low medium pressure flows through the inne...
Embodiment 3
[0033] Example 3, on the basis of Example 2, the mutual positional relationship between the barrel section A4-3 and the barrel section B5-3 is optimized, wherein the barrel section A4-3 and the barrel section B5-3 are concentrically arranged, and the barrel section A4-3 is arranged concentrically with the barrel section A4 -3 and the barrel section B5-3 are respectively connected to the annular sealing surface A and the annular sealing surface B on the tube sheet 3, which are also arranged concentrically with each other, that is, the barrel section A4-3, the barrel section B5-3, the annular The concentric arrangement of the sealing surface A3-1 and the annular sealing surface B3-2 is conducive to maintaining the stability of the flow drainage of the two parts of the pipe box, and it is easy to balance the pressure of the pipe box process, reducing the impact on the unbalanced pressure of the pipe box structure Security Risk. The pipes of the inner and outer tubes are arranged ...
Embodiment 4
[0034] Embodiment 4, on the basis of Embodiment 1, the location of the manhole 6 is optimized, wherein the manhole 6 is located at the position of the barrel section A4-3 of the outer tube box 4 and the connecting pipe B5-1 is at the barrel section of the outer tube box 4 The lead-out position on A4-3 is right, so that it is convenient for inspectors to check the sealing of the connection parts between the inner and outer tube boxes and the annular sealing surface one by one in the left and right directions after entering the outer tube box 4 through the manhole 6, and divide them equally. The inspection surfaces on both sides of the tube box, especially the heat exchange tubes in the outer tube box process leak, the maintenance personnel can directly open the manhole 6 and enter the outer tube box 4 to quickly perform leak detection, maintenance and other operations, and can quickly and automatically The manhole 6 on the outer tube box 4 is withdrawn.
PUM
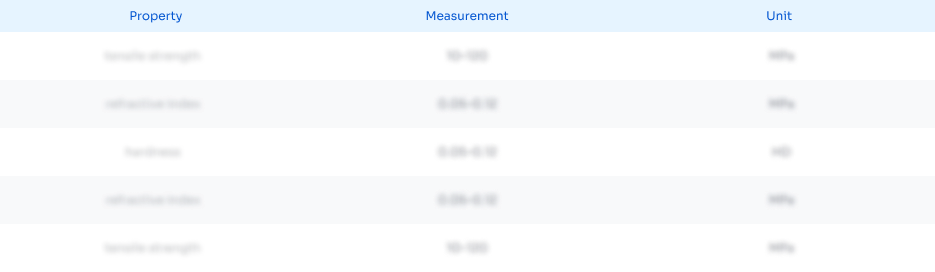
Abstract
Description
Claims
Application Information

- R&D
- Intellectual Property
- Life Sciences
- Materials
- Tech Scout
- Unparalleled Data Quality
- Higher Quality Content
- 60% Fewer Hallucinations
Browse by: Latest US Patents, China's latest patents, Technical Efficacy Thesaurus, Application Domain, Technology Topic, Popular Technical Reports.
© 2025 PatSnap. All rights reserved.Legal|Privacy policy|Modern Slavery Act Transparency Statement|Sitemap|About US| Contact US: help@patsnap.com