Control method, equipment, system and construction machinery for multi-joint mechanical arm support
A robotic arm, multi-joint technology, applied in mechanically driven excavators/dredgers, mining equipment, cranes, etc., can solve the problems that the end of the multi-joint boom cannot be accurately reached and the operation efficiency is low.
- Summary
- Abstract
- Description
- Claims
- Application Information
AI Technical Summary
Problems solved by technology
Method used
Image
Examples
Embodiment 1
[0041] Such as figure 2 As shown, it is a flowchart of a control method of a multi-joint mechanical arm frame according to Embodiment 1 of the present invention, and the method includes:
[0042] Step 101: Divide the trajectory path of the end movement of the mechanical arm frame into N sub-trajectory paths by using the set method of simulating the end movement of the mechanical arm frame.
[0043] Wherein, N is a positive integer not less than 1.
[0044] In step 101, before the discrete operation is performed on the trajectory path of the movement of the end of the mechanical arm, the method further includes: determining the movement trajectory of the end of the mechanical arm.
[0045] Specifically, the method for determining the moving trajectory path of the end of the mechanical arm includes but is not limited to: determining according to the current position information of the end of the mechanical arm and the target position to which it moves.
[0046] After the trajec...
Embodiment 2
[0101] Such as image 3 As shown, it is a schematic structural diagram of a control device of a multi-joint mechanical arm frame according to Embodiment 2 of the present invention, the device includes: a discrete processing module 11 and a control module 12, wherein:
[0102] The discrete processing module 11 is used to divide the trajectory path of the end movement of the mechanical arm frame into N sub-trajectory paths by using the set method of simulating the end movement of the mechanical arm frame, where N is a positive integer not less than 1;
[0103] The control module 12 is configured to perform the following operations on each sub-track path except the obtained first sub-track path:
[0104] Calculate the displacement linear velocity, displacement linear acceleration and The length value that the end of the current robotic arm can move within the set time period;
[0105] Collect the current position information of each joint of the mechanical arm frame, and use th...
Embodiment 3
[0130] Such as Figure 4 As shown, it is a schematic structural diagram of a control system of a multi-joint mechanical arm frame according to Embodiment 3 of the present invention. The system includes: acquisition equipment 31, control equipment 32 and electro-hydraulic proportional valve 33, wherein:
[0131] The collecting device 31 is used to collect the current position information of each joint of the mechanical arm frame.
[0132] The control device 32 is used to divide the trajectory path of the end movement of the mechanical arm frame into N sub-trajectory paths by using the set method of simulating the end movement of the mechanical arm frame, where N is a positive integer not less than 1;
[0133] For each sub-trajectory path except the obtained first sub-trajectory path, the following operations are performed respectively: the target displacement distance, actual displacement distance, displacement linear velocity and Displacement linear acceleration, calculate th...
PUM
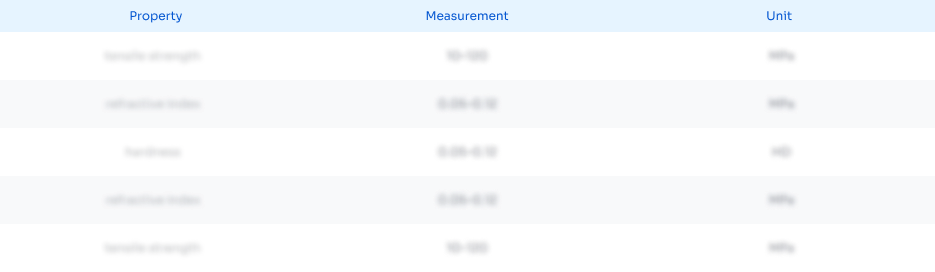
Abstract
Description
Claims
Application Information

- R&D
- Intellectual Property
- Life Sciences
- Materials
- Tech Scout
- Unparalleled Data Quality
- Higher Quality Content
- 60% Fewer Hallucinations
Browse by: Latest US Patents, China's latest patents, Technical Efficacy Thesaurus, Application Domain, Technology Topic, Popular Technical Reports.
© 2025 PatSnap. All rights reserved.Legal|Privacy policy|Modern Slavery Act Transparency Statement|Sitemap|About US| Contact US: help@patsnap.com