Composition as well as preparation method and application thereof
A technology of composition and application, applied in the field of high temperature resistant atomized materials, can solve the problem of formula to be improved, and achieve the effect of saving time and resources and improving efficiency
- Summary
- Abstract
- Description
- Claims
- Application Information
AI Technical Summary
Problems solved by technology
Method used
Image
Examples
Embodiment 1
[0035] Example 1: Preparation of sheet and front fog lamp rear cover
[0036] Mixing: Weigh 100 parts of raw material EPDM and put it into the open mill; plasticize for 5 minutes, then put in 30 parts of N330 carbon black, 35 parts of N550 carbon black, 6 parts of active zinc oxide, 0.5 part of stearic acid, and RD3 antioxidant 2 parts of anti-fogging wax, 1.2 parts of rubber dispersant and 12 parts of softener, knead for 8 minutes, and clean and tumble once every 3 minutes during this period; the discharge temperature reaches 115°C, and the total mixing time is 13 minutes to obtain good banburying glue;
[0037] Opening: Cool the lower piece of the mixed rubber material, the roller distance is 5-6mm, add 4.5 parts of DCP, 0.45 parts of vulcanizing agent POM, and the roller distance is 5-6mm, after making 2 triangle bags, thin pass 1 time, and then make 2 triangle bags, the roller distance is 0.5-1.0mm, and the film is produced.
[0038] Product processing: temperature: 170...
Embodiment 2
[0040] Example 2: Preparation of sheet and front fog lamp rear cover
[0041] Mixing: Weigh 99.5 parts of raw material EPDM and put it into the open mill; plasticize for 5 minutes, then put in 29.5 parts of N330 carbon black, 34.5 parts of N550 carbon black, 5.99 parts of active zinc oxide, 0.49 parts of stearic acid, and RD2 antioxidant .99 parts, 1.99 parts of anti-fog wax, 1.19 parts of rubber dispersant and 11.5 parts of softener, kneaded for 8 minutes, and cleaned and rolled every 3 minutes during this period; the discharge temperature reached 110 ° C, and the total time of kneading was 13 minutes to obtain dense Refined rubber;
[0042] Opening: Cool the lower piece of the mixed rubber material, the roller distance is 5-6mm, add 4.495 parts of DCP, 0.445 parts of vulcanizing agent POM, the roller distance is 5-6mm, make 2 triangular bags, thin pass 1 time, and then make 2 triangle bags, the roller distance is 0.5-1.0mm, and the film is produced.
[0043] Product proces...
Embodiment 3
[0045] Example 3: Preparation of sheet and front fog lamp rear cover
[0046] Mixing: Weigh 100.5 parts of raw material EPDM and put it into the open mill; plasticize for 5 minutes, then put in 30.5 parts of N330 carbon black, 35.5 parts of N550 carbon black, 6.01 parts of active zinc oxide, 0.51 parts of stearic acid, and RD3 antioxidant .01 parts, 2.01 parts of anti-fog wax, 1.21 parts of rubber dispersant and 12.5 parts of softener, kneaded for 8 minutes, and cleaned and rolled every 3 minutes during this period; the discharge temperature reached 120 ° C, and the total mixing time was 13 minutes to obtain dense Refined rubber;
[0047] Opening: Cool the lower piece of the mixed rubber material, the roller distance is 5-6mm, add 4.505 parts of DCP, 0.455 parts of vulcanizing agent POM, the roller distance is 5-6mm, make 2 triangular bags, thin pass 1 time, and then make 2 triangle bags, the roller distance is 0.5-1.0mm, and the film is produced.
[0048] Product processing...
PUM
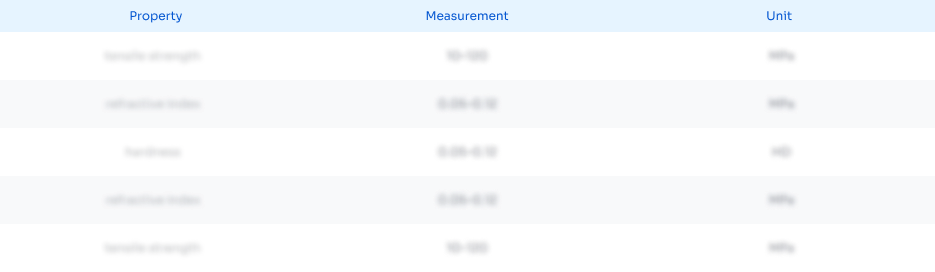
Abstract
Description
Claims
Application Information

- Generate Ideas
- Intellectual Property
- Life Sciences
- Materials
- Tech Scout
- Unparalleled Data Quality
- Higher Quality Content
- 60% Fewer Hallucinations
Browse by: Latest US Patents, China's latest patents, Technical Efficacy Thesaurus, Application Domain, Technology Topic, Popular Technical Reports.
© 2025 PatSnap. All rights reserved.Legal|Privacy policy|Modern Slavery Act Transparency Statement|Sitemap|About US| Contact US: help@patsnap.com