Technological method for symmetrical paired universal rolling of deformed steel
A technology of universal rolling and process method, applied in the direction of metal rolling, etc., can solve the problem of increasing the number of cutting heads/tails of cold saw cut-to-length sawing, increasing the blind area of the head/tail of straightening rolled pieces, and more short-length rolled pieces on the cooling bed, etc. problems, to achieve the effect of comprehensive processing quality and mechanical properties, good surface quality, and small internal stress of the rolled piece
- Summary
- Abstract
- Description
- Claims
- Application Information
AI Technical Summary
Problems solved by technology
Method used
Image
Examples
Embodiment 1
[0036] Such as figure 1 and figure 2 Shown, the processing method of special-shaped steel symmetrical double universal rolling of the present invention comprises the following steps:
[0037] 1) In the rough rolling unit, the original billet is rough-rolled by a two-roller edger in a plane-symmetric form to form an intermediate billet of a double conjoined rolling piece;
[0038] 2) The irregularly deformed head and tail of the intermediate blank are cut off by sawing facilities;
[0039] 3) In the finish rolling unit, the intermediate billet is simultaneously universally rolled by a universal rolling mill and a two-roll edger in a face-symmetrical double-jointed body, and finished rolling into a double-joined final cross-section profile;
[0040] 4) The profile rolled into the final section of the double conjoined body is cooled to room temperature, first divided into single rolled pieces by the splitting facility, and then straightened by the straightening facility to str...
Embodiment 2
[0042] Such as figure 1 and figure 2 Shown, the processing method of special-shaped steel symmetrical double universal rolling of the present invention comprises the following steps:
[0043] 1) Roughly roll the original billet in the rough rolling unit through a four-high universal rolling mill in a plane-symmetrical form to form an intermediate billet of a double conjoined rolling piece;
[0044] 2) The irregularly deformed head and tail of the intermediate blank are cut off by sawing facilities;
[0045] 3) In the finish rolling unit, the intermediate billet is simultaneously universally rolled by a universal rolling mill and a two-roll edger in a face-symmetrical double-jointed body, and finished rolling into a double-joined final cross-section profile;
[0046] 4) The profile rolled into a double-jointed final section is cooled to room temperature, and the profile is first straightened by a straightening facility, and then divided into two single-rolled pieces by a spl...
Embodiment 3
[0048] Such as image 3 and Figure 4 Shown, the processing method of special-shaped steel symmetrical double universal rolling of the present invention comprises the following steps:
[0049] 1) In the rough rolling unit, the original billet is rough-rolled by a two-roller edger in an axisymmetric form to form an intermediate billet of a double conjoined rolling piece;
[0050] 2) The irregularly deformed head and tail of the intermediate blank are cut off by sawing facilities;
[0051] 3) In the finish rolling unit, the intermediate billet is simultaneously universally rolled by a universal rolling mill and a two-roll edger in an axisymmetric double-jointed body, and finished into a double-jointed final section profile;
[0052] 4) The profile rolled into the final section of the double conjoined body is cooled to room temperature, first divided into single rolled pieces by the splitting facility, and then straightened by the straightening facility to straighten the two si...
PUM
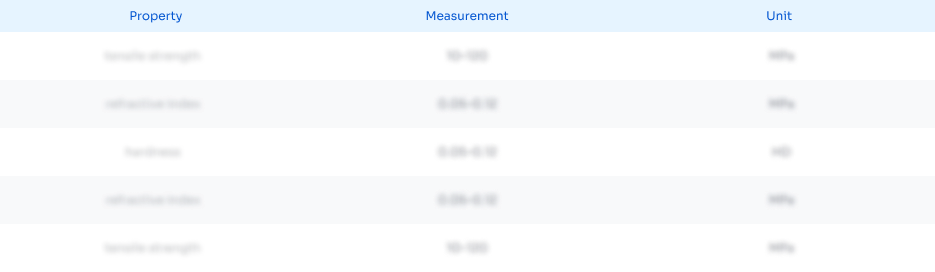
Abstract
Description
Claims
Application Information

- R&D
- Intellectual Property
- Life Sciences
- Materials
- Tech Scout
- Unparalleled Data Quality
- Higher Quality Content
- 60% Fewer Hallucinations
Browse by: Latest US Patents, China's latest patents, Technical Efficacy Thesaurus, Application Domain, Technology Topic, Popular Technical Reports.
© 2025 PatSnap. All rights reserved.Legal|Privacy policy|Modern Slavery Act Transparency Statement|Sitemap|About US| Contact US: help@patsnap.com