Fabric as combustor covering, and its making method
A covering and burner technology, applied in textiles and papermaking, fabric surface trimming, yarn, etc., can solve the problems of poor infrared quality, easy tempering, slow infrared response, etc., and achieve infrared performance and anti-tempering ability Optimized and better infrared burning effect
- Summary
- Abstract
- Description
- Claims
- Application Information
AI Technical Summary
Problems solved by technology
Method used
Image
Examples
Embodiment 1
[0078] 1. Using the core spinning method, the 50-micron iron-chromium-aluminum metal monofilament (that is, the metal fiber filament 12, the same below) is spun into about 60 pounds of polyester spun yarn (that is, the isolation fiber 14) through the spinning machine. ) with a twist of 400 twists / m to obtain a metal fiber composite monofilament.
[0079] 2. Use a twisting machine to twist 30 such metal fiber composite monofilaments to obtain a 30*1 composite yarn, or to obtain a 15*2 composite yarn by twisting twice; by analogy, Metal fiber composite yarn 15 with fewer single yarn cores and more strands can be obtained by twisting multiple times, see Figure 15 . Among them, in order to maintain a good dispersion effect and weaving stability, the metal fiber composite yarn is preferably twisted at 20-80 twists / m, and the twist of the initial twist can be different.
[0080] 3. Using a 5-needle flat knitting machine, weave the composite yarn into a stable structure fabric wit...
Embodiment 2
[0083] 1. Adopt the coating method, coat the water-soluble spun yarn of about 100 lbs on the 40-micron iron-chromium-aluminum metal monofilament, with a twist of 400 twists / meter, to obtain the metal fiber composite monofilament (see Figure 16-1 ).
[0084] 2. Twist 50 such composite monofilaments through a twisting machine to obtain a 50*1 composite yarn, or obtain a 25*2 composite yarn by twisting twice (see Figure 16-2 ); By analogy, metal fiber composite yarns with fewer single yarn cores and more strands can be obtained by twisting multiple times. In order to maintain a good dispersion effect and weaving stability, it is preferable to twist at 20-80 twists / meter, and the twist degree of the initial twist can be different.
[0085] 3. Use a 7-needle flat knitting machine to weave the composite yarn into a stable structure fabric with a certain thickness (see Figure 17 ).
[0086] 4. Through rolling, the thickness of the composite fabric is thinned, and part of the ya...
Embodiment 3
[0089] 1. Using a twisting machine, twist the 50-micron iron-chromium-aluminum metal monofilament and the 60-tex polyester filament with a twist degree of 200 twists / m to obtain a metal fiber composite monofilament.
[0090] 2. Through the twisting machine, twist 40 such composite monofilaments to obtain a 40*1 composite yarn, or obtain a 25*2 composite yarn by twisting twice; by analogy, you can use Multi-twisting to obtain a metal fiber composite yarn with fewer single yarn cores and more strands. In order to maintain a good dispersion effect and weaving stability, it is preferable to twist at 20-80 twists / meter, and the twist degree of the initial twist can be different.
[0091] 3. Using a 7-needle flat knitting machine, weave the composite yarn into a stable structure fabric with a certain thickness.
[0092] 4. Soak the composite fabric in concentrated sulfuric acid, partially or completely remove the insulating material components in the composite fabric, wash and dry....
PUM
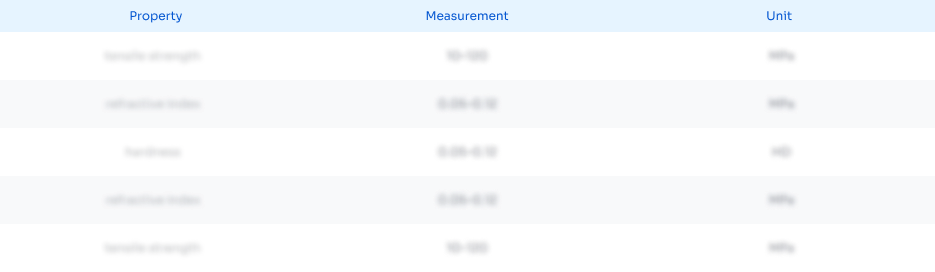
Abstract
Description
Claims
Application Information

- Generate Ideas
- Intellectual Property
- Life Sciences
- Materials
- Tech Scout
- Unparalleled Data Quality
- Higher Quality Content
- 60% Fewer Hallucinations
Browse by: Latest US Patents, China's latest patents, Technical Efficacy Thesaurus, Application Domain, Technology Topic, Popular Technical Reports.
© 2025 PatSnap. All rights reserved.Legal|Privacy policy|Modern Slavery Act Transparency Statement|Sitemap|About US| Contact US: help@patsnap.com