Granulating process of thermosetting phenolic resin for stored energy electrical carbon
A phenolic resin and thermosetting technology, which is applied in the field of new carbon material preparation, can solve the problems of easy bonding of particle balls, uneven performance of electric carbon materials, and inability to mix raw materials evenly, so as to achieve low labor cost, high productivity and high output. big effect
- Summary
- Abstract
- Description
- Claims
- Application Information
AI Technical Summary
Problems solved by technology
Method used
Examples
Embodiment 1
[0019] First, mix the thermosetting phenolic resin, curing agent, and latent curing agent according to the weight ratio of 1:0.05:0.20, then add it to a high-speed crusher and crush it into a 100-mesh fine powder, wherein the curing agent is urotropine, and the latent curing agent is bisphenol A phenolic resin; then, chlorinated polyethylene and ammonium hydrogen phosphate are added into the high-speed mixer together with the fine powder as a slow curing agent and mixed, and after mixing evenly, the material automatically enters the twin-screw extruder for extrusion and granulation. The diameter of the die head of the screw extruder is 2mm, the internal temperature is 120°C, and the back pressure is 4MPa, and high-speed cold air is introduced to cool the pellets to prevent the pellets from sticking when the extrusion die is cut and granulated; The conveying pipeline connected to the outlet of the twin-screw extruder transports the pellets in a cold air environment, and collects...
Embodiment 2
[0021] First, mix the thermosetting phenolic resin, curing agent, and latent curing agent according to the weight ratio of 1:0.10:0.15, then add it to a high-speed crusher and crush it into a 200-mesh fine powder. Oxygen resin; then add phenol as slow curing agent and fine powder together to the high-speed mixer for mixing, and after mixing evenly, the material will automatically enter the twin-screw extruder for extrusion and granulation. The die head aperture of the twin-screw extruder 5㎜, internal temperature 250°C, back pressure 12 MPa, and high-speed cold air is passed through the extrusion die to cool the pellets to prevent pellets from sticking; it is connected to the outlet of the twin-screw extruder Through the conveying pipeline, the pellets are transported in a cold air environment, and the pellets of thermosetting phenolic resin for energy storage electric carbon are collected. The granulation process of the present invention can make the raw materials of electric ...
Embodiment 3
[0023] First, mix the thermosetting phenolic resin, curing agent, and latent curing agent according to the weight ratio of 1:0.08:0.12, then add it to a high-speed crusher and crush it into a 225-mesh fine powder, wherein the curing agent is urotropine, and the latent curing agent is bisphenol A phenolic resin; then add ammonium hydrogen phosphate, phenol and p-toluenesulfonic acid as slow curing agent together with fine powder into the high-speed mixer and mix, after mixing evenly, the material will automatically enter the twin-screw extruder for extrusion and granulation The diameter of the die head of the twin-screw extruder is 3 mm, the internal temperature is 150 ° C, and the back pressure is 7 MPa. When the extrusion die is cut and granulated, high-speed cold air is introduced to cool the pellets to prevent the pellets from sticking. The conveying pipeline connected with the outlet of the twin-screw extruder transports the pellets in a cold air environment, and collects t...
PUM
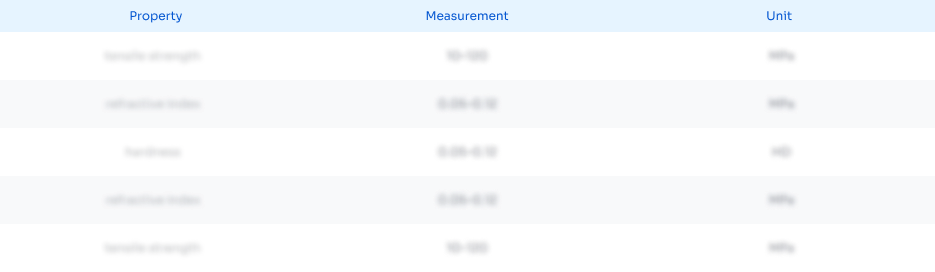
Abstract
Description
Claims
Application Information

- R&D Engineer
- R&D Manager
- IP Professional
- Industry Leading Data Capabilities
- Powerful AI technology
- Patent DNA Extraction
Browse by: Latest US Patents, China's latest patents, Technical Efficacy Thesaurus, Application Domain, Technology Topic, Popular Technical Reports.
© 2024 PatSnap. All rights reserved.Legal|Privacy policy|Modern Slavery Act Transparency Statement|Sitemap|About US| Contact US: help@patsnap.com