Roll shaft type metal shock-insulating supporting seat
A technology of seismic isolation bearings and roller shafts, which is applied in the direction of earthquake resistance, building components, construction, etc., can solve problems such as failure of seismic isolation bearings, prolonging the equivalent period, and weak tensile strength, so as to protect the upper structure and structure The effect of period extension and obvious vibration isolation effect
- Summary
- Abstract
- Description
- Claims
- Application Information
AI Technical Summary
Problems solved by technology
Method used
Image
Examples
Embodiment 1
[0038] figure 1 It is a schematic diagram of the structure of this embodiment. This embodiment consists of an upper connecting plate 1, a roller shaft 2, a roller frame 3, an intermediate end plate 4, an L-shaped tensile connecting plate 5, a pre-tightening pad 6, a polytetrafluoroethylene plate 7, and a lower connecting plate 8 , 9 friction-type high-strength bolts, 10 high-strength tensile bolts. During assembly, a plurality of roller shafts 2 are installed in the roller frame 3 earlier, and the cylindrical supports 13 at both ends of the rollers extend into the cylindrical holes 14 of the roller frame, and the positions where the two contact are lubricated with lubricant. The roller set is placed in the rolling groove 12 of the middle end plate 4 . The middle end plate 4 and the upper connecting plate 1 are fixed through the L-shaped tensile connecting plate 5, and the friction type high-strength bolts 9 are used for the connection. The side of the L-shaped tensile connec...
Embodiment 2
[0048] Figure 10 It is the specific structure schematic diagram of this embodiment. Balls 20 are set between the upper connecting plate 1, the lower connecting plate 8 and the pre-tightening force backing plate 6, and the ball rolling grooves 21, 22 are set on the upper connecting plate 1, the lower connecting plate 8 and the pre-tightening force backing plate 6. The rolling of the ball replaces the sliding of the PTFE plate, which further reduces the friction force and horizontal stiffness during tension, and can be used for structures with lower rigidity requirements during tension. The diameter and number of balls can be set according to the tensile bearing capacity. fixed, for a structure with a large tensile bearing capacity, the ball can also be replaced by a roller shaft. At this time, the length of the roller shaft is smaller than the length of the pressure roller shaft. The effect of the compressive bearing capacity is much larger than the tensile bearing capacity, ...
Embodiment 3
[0051] Figure 12 It is the specific structure schematic diagram of this embodiment. Paste polytetrafluoroethylene plates 23 on the contact surfaces of the upper and lower connecting plates 1, 8 and the middle end plate 4, and use the sliding between the polytetrafluoroethylene plates to reduce the seismic force and achieve the effect of shock isolation. This embodiment is especially suitable In the case of small installation space and high bearing capacity. Since the sliding friction between the PTFE plates is used for shock isolation, the friction coefficient is larger than the rolling friction of the roller shaft, and the shock isolation effect is slightly worse. However, due to the pressure or tension on the contact surface, its vertical bearing capacity Much bigger. Other structures of this embodiment are the same as those of Embodiment 1.
[0052] Figure 13 It is a schematic diagram of the polytetrafluoroethylene plate of the present embodiment.
PUM
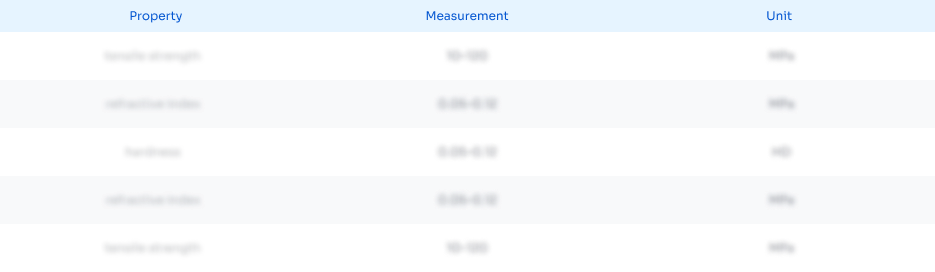
Abstract
Description
Claims
Application Information

- R&D
- Intellectual Property
- Life Sciences
- Materials
- Tech Scout
- Unparalleled Data Quality
- Higher Quality Content
- 60% Fewer Hallucinations
Browse by: Latest US Patents, China's latest patents, Technical Efficacy Thesaurus, Application Domain, Technology Topic, Popular Technical Reports.
© 2025 PatSnap. All rights reserved.Legal|Privacy policy|Modern Slavery Act Transparency Statement|Sitemap|About US| Contact US: help@patsnap.com