Production method of melamine by slow cooling crystallization
A technology of melamine and production methods, applied in the direction of sustainable manufacturing/processing, chemical industry, climate sustainability, etc., can solve the problems of high bituminous coal consumption, large system resistance, large power consumption, etc., and achieve saving power consumption and electricity consumption Effects of reduced coal consumption and reduced system resistance
- Summary
- Abstract
- Description
- Claims
- Application Information
AI Technical Summary
Problems solved by technology
Method used
Image
Examples
Embodiment Construction
[0022] The molten urea is pumped to the urea adding port of the reactor through the urea pump, atomized under the action of the atomizing gas and enters the reactor, under the pressure range from normal pressure to <10MPa and at a high temperature of 390°C, it is reacted and formed by the action of a catalyst Melamine. The heat required for the reaction is provided by the molten salt system. The carrier gas of the fluidized bed comes from the purified and separated reaction tail gas, mainly a mixture of ammonia and carbon dioxide. After the carrier gas compressor is boosted, it is exchanged with the outlet gas of the reactor through a heat exchanger. Heat, and then enter the carrier gas preheater, heated by molten salt to 360-410°C, and then enter the bottom inlet of the reactor.
[0023] The reacted gas enters the heat exchange system to heat the carrier gas at the inlet of the reactor, and its own temperature can be reduced by 310-330°C. The high-boiling point by-products of...
PUM
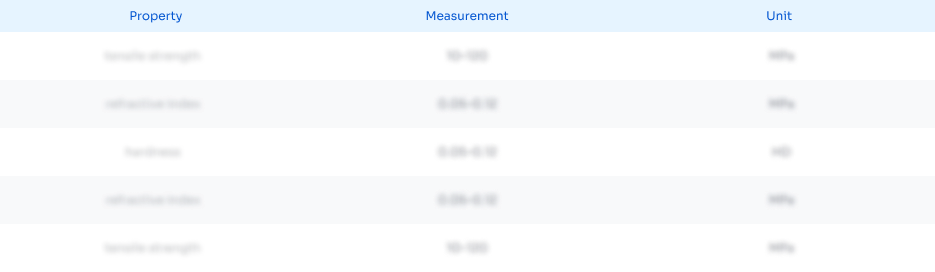
Abstract
Description
Claims
Application Information

- R&D Engineer
- R&D Manager
- IP Professional
- Industry Leading Data Capabilities
- Powerful AI technology
- Patent DNA Extraction
Browse by: Latest US Patents, China's latest patents, Technical Efficacy Thesaurus, Application Domain, Technology Topic, Popular Technical Reports.
© 2024 PatSnap. All rights reserved.Legal|Privacy policy|Modern Slavery Act Transparency Statement|Sitemap|About US| Contact US: help@patsnap.com