Preparation method of epoxy resin-modified polyurethane emulsion leather finishing agent
A technology of polyurethane emulsion and leather finishing agent, which is applied in the field of leather chemistry, can solve the problems of insufficient adhesion, leveling, and hygienic performance that cannot meet people's requirements, and achieve the effect of promoting firm bonding, high strength, and simple process
- Summary
- Abstract
- Description
- Claims
- Application Information
AI Technical Summary
Problems solved by technology
Method used
Examples
Embodiment 1-1
[0017] Dehydrate 3kg of polyoxyethylene diol under vacuum at 110°C for 1h, then lower the temperature to 50°C; add 1kg of toluene diisocyanate and 1g of dibutyltin dilaurate under nitrogen protection, and react at 75°C for 3h , then lower the temperature to 30°C; add 500g epoxy resin E-12, 300g N-methyldiethanolamine, react at 60°C for 4h, then lower the temperature to 40°C; add glacial acetic acid to adjust the pH value to 6, then Add 10kg of acetone for dilution, then add 10kg of deionized water for high-speed emulsification, vacuum remove the acetone solvent to obtain an epoxy resin modified cationic polyether polyurethane emulsion.
Embodiment 2-1
[0019] Dehydrate 4kg of polyoxyethylene diol under vacuum at 120°C for 2h, then lower the temperature to 70°C; add 1.5kg of toluene diisocyanate and 50g of stannous octoate under nitrogen protection, react at 85°C for 2h, and then Lower the temperature to 40°C; add 1kg epoxy resin E-20, 600g N-methyldiethanolamine, react at 65°C for 2 hours, then lower the temperature to 50°C; add glacial acetic acid to adjust the pH to 7, then add 2kg of acetone Dilute, then add 8 kg of deionized water for high-speed emulsification, and vacuum remove the acetone solvent to obtain an epoxy resin-modified cationic polyether polyurethane emulsion.
Embodiment 3-1
[0021] Dehydrate 3.5kg of polyoxyethylene diol under vacuum at 115°C for 1.5h, then lower the temperature to 60°C; add 1.2kg of toluene diisocyanate and 5g of stannous octoate under nitrogen protection, and react at 80°C for 2.5h , then lower the temperature to 35°C; add 600g epoxy resin E-42, 400g N-methyldiethanolamine, react at 62°C for 3h, then lower the temperature to 45°C; add glacial acetic acid to adjust the pH value to 5, then Add 5kg of acetone for dilution, then add 9kg of deionized water for high-speed emulsification, vacuum remove the acetone solvent to obtain an epoxy resin modified cationic polyether polyurethane emulsion.
PUM
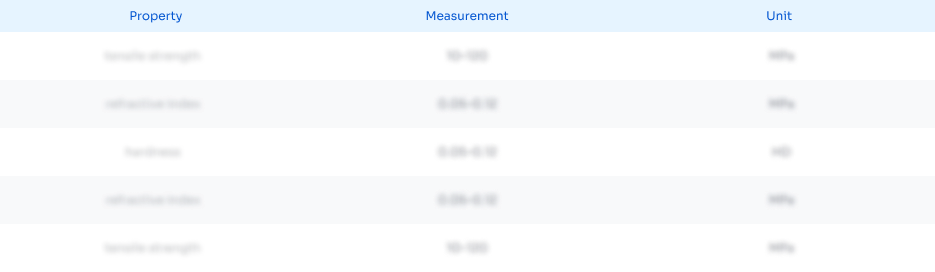
Abstract
Description
Claims
Application Information

- R&D
- Intellectual Property
- Life Sciences
- Materials
- Tech Scout
- Unparalleled Data Quality
- Higher Quality Content
- 60% Fewer Hallucinations
Browse by: Latest US Patents, China's latest patents, Technical Efficacy Thesaurus, Application Domain, Technology Topic, Popular Technical Reports.
© 2025 PatSnap. All rights reserved.Legal|Privacy policy|Modern Slavery Act Transparency Statement|Sitemap|About US| Contact US: help@patsnap.com