Vertical injection molding machine
An injection molding machine, vertical technology, applied in the field of vertical injection molding machines, can solve the problems of unbalanced mold clamping, high labor intensity, cumbersome mechanism, etc. Effect
- Summary
- Abstract
- Description
- Claims
- Application Information
AI Technical Summary
Problems solved by technology
Method used
Image
Examples
Embodiment 1
[0040] An enterprise in Nanning City, Guangxi, adopts vertical injection molding of the present invention to make plastic rose petals, see attached figure 1 , Image 6 with Figure 7 shown. The process is as follows: first, put loose granular or granular plastic materials into the feeding hopper 15 of the feeding mechanism 4, turn on the power, start the feeding motor 19, and send the raw materials into the injection barrel 5 for heating and melting. Press the mold clamping button, the mold clamping solenoid valve on the hydraulic manifold 21 is switched on, the hydraulic system pushes the piston rod of the mold clamping cylinder installed on the bottom plate forward, drives the mold clamping mechanism 14, drives the guided cross 30, and pushes the The connecting rod 26 and the short connecting rod 27 move forward around the hinge point, so that the movable platen 9 moves along the guide column 8 to the direction of the fixed platen 6 until the mold is closed. A signal is s...
PUM
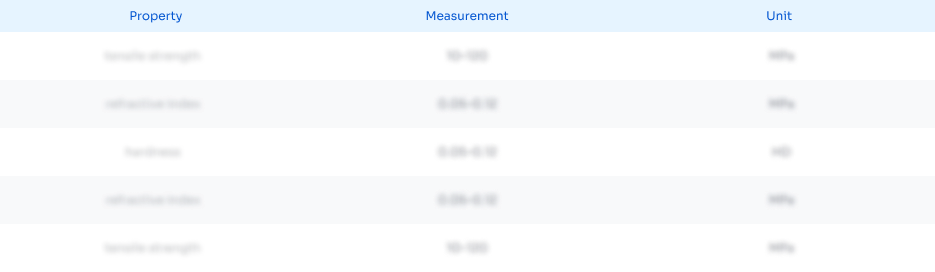
Abstract
Description
Claims
Application Information

- R&D
- Intellectual Property
- Life Sciences
- Materials
- Tech Scout
- Unparalleled Data Quality
- Higher Quality Content
- 60% Fewer Hallucinations
Browse by: Latest US Patents, China's latest patents, Technical Efficacy Thesaurus, Application Domain, Technology Topic, Popular Technical Reports.
© 2025 PatSnap. All rights reserved.Legal|Privacy policy|Modern Slavery Act Transparency Statement|Sitemap|About US| Contact US: help@patsnap.com