Reduction steel-making method and reduction steel-marking device
A steelmaking furnace and molten steel technology, applied in the field of metallurgy, can solve the problems of increasing energy consumption, oxygen consumption, increasing greenhouse gas emissions, waste of resources, etc., and achieve the effect of reducing intermediate material reverse transportation, reducing consumption, and reducing land occupation
- Summary
- Abstract
- Description
- Claims
- Application Information
AI Technical Summary
Problems solved by technology
Method used
Image
Examples
Embodiment 1
[0027] Such as figure 1 Shown is a schematic structural view of a reduction steelmaking device of the present invention; as figure 2 Shown is a structural schematic diagram of a reduction steelmaking furnace with a bottom blowing system in a reduction steelmaking device of the present invention; as image 3 Shown is a structural schematic diagram of a reduction steelmaking furnace with a side blowing system in a reduction steelmaking device of the present invention;
[0028] A kind of reduction steelmaking method of the present invention, its step is as follows:
[0029] 1) Put the iron ore material into the reducing steelmaking furnace 6, and blow reducing gas into the reducing steelmaking furnace 6 at the same time, and the reducing gas is heated by the electric arc or plasma arc generated by the electrode 4 to form a high temperature reducing gas at 800°C to 9700°C , the iron ore and the high-temperature reducing gas are subjected to an initial reduction reaction in the ...
PUM
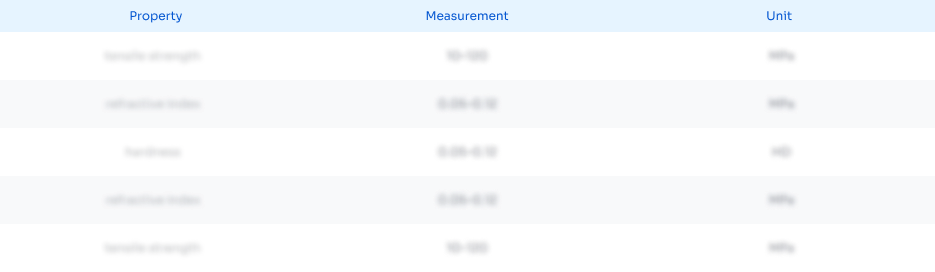
Abstract
Description
Claims
Application Information

- R&D
- Intellectual Property
- Life Sciences
- Materials
- Tech Scout
- Unparalleled Data Quality
- Higher Quality Content
- 60% Fewer Hallucinations
Browse by: Latest US Patents, China's latest patents, Technical Efficacy Thesaurus, Application Domain, Technology Topic, Popular Technical Reports.
© 2025 PatSnap. All rights reserved.Legal|Privacy policy|Modern Slavery Act Transparency Statement|Sitemap|About US| Contact US: help@patsnap.com