Method for preparing isobutylene by dehydrogenizing iso-butane
A technology of isobutane and isobutene, which is applied in the field of isobutene preparation, can solve problems such as complex process flow and loss of raw material isobutane, and achieve the effects of simplifying process flow, reducing raw material loss, easy control and smooth operation
- Summary
- Abstract
- Description
- Claims
- Application Information
AI Technical Summary
Problems solved by technology
Method used
Image
Examples
Embodiment 1
[0015] Preparation of solid Cr by a solid-state ion exchange 2 o 3 –CaO-K 2 O-Al 2 o 3 As a catalyst, at a reaction temperature of 530°C, a reaction pressure of 0.2MPa, and a reaction mass space velocity of 1.0h -1 Under the conditions, after the dehydrogenation reaction for 5 minutes, stop the reaction raw material isobutane feed under the same reaction conditions, feed hydrogen into the reactor at a rate of 10:1 by hydrogen volume space velocity, and carry out hydrogen reduction regeneration on the catalyst The ratio of the hydrogen reduction regeneration time to the reaction time is controlled at 1:1, that is, the hydrogen reduction is 5 minutes; after the hydrogen reduction regeneration is completed, the hydrogen feeding is stopped, and the raw material isobutane feeding is switched, and the cycle is repeated. The reaction product was collected with an air bag and analyzed by gas chromatography. The results are shown in Table 1.
Embodiment 2
[0017] Preparation of solid Cr by a solid-state ion exchange 2 o 3 –CaO-K 2 O-Al 2 o 3 As a catalyst, at a reaction temperature of 550°C, a reaction pressure of 0.1MPa, and a reaction mass space velocity of 1.0h -1 Under the conditions, after the dehydrogenation reaction for 10 minutes, stop the reaction raw material isobutane feed under the same reaction conditions, feed hydrogen into the reactor at the rate of hydrogen volume space velocity 100:1, and carry out hydrogen reduction regeneration of the catalyst The ratio of the hydrogen reduction regeneration time to the reaction time is controlled at 2:1, that is, the hydrogen reduction is 20 minutes; after the hydrogen reduction regeneration is completed, the hydrogen feed is stopped, and the raw material isobutane feed is switched, and the cycle is repeated. The reaction product was collected with an air bag and analyzed by gas chromatography. The results are shown in Table 1.
Embodiment 3
[0019] Preparation of solid Cr by a solid-state ion exchange 2 o 3 –CaO-K 2 O-Al 2 o 3 As a catalyst, at a reaction temperature of 580°C, a reaction pressure of 0.5MPa, and a reaction mass space velocity of 1.5h -1 Under the conditions, after the dehydrogenation reaction for 15 minutes, stop the reaction raw material isobutane feed under the same reaction conditions, feed hydrogen into the reactor at the rate of hydrogen volume space velocity 200:1, and regenerate the catalyst with hydrogen reduction The ratio of the hydrogen reduction regeneration time to the reaction time is controlled at 2:1, that is, the hydrogen reduction is 30 minutes; after the hydrogen reduction regeneration is completed, the hydrogen feed is stopped, and the raw material isobutane feed is switched, and the cycle is repeated. The reaction product was collected with an air bag and analyzed by gas chromatography. The results are shown in Table 1.
PUM
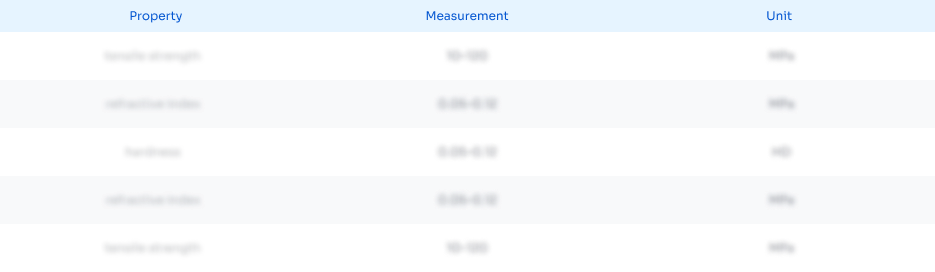
Abstract
Description
Claims
Application Information

- Generate Ideas
- Intellectual Property
- Life Sciences
- Materials
- Tech Scout
- Unparalleled Data Quality
- Higher Quality Content
- 60% Fewer Hallucinations
Browse by: Latest US Patents, China's latest patents, Technical Efficacy Thesaurus, Application Domain, Technology Topic, Popular Technical Reports.
© 2025 PatSnap. All rights reserved.Legal|Privacy policy|Modern Slavery Act Transparency Statement|Sitemap|About US| Contact US: help@patsnap.com