Automatic winding control system for wide lead tape production line
An automatic control system and control system technology, applied in the direction of winding strips, thin material processing, transportation and packaging, etc., can solve problems that affect product quality, unfavorable production development of enterprises, and reduce work efficiency, so as to achieve a short period of transformation and production , Conducive to production development, high response speed effect
- Summary
- Abstract
- Description
- Claims
- Application Information
AI Technical Summary
Problems solved by technology
Method used
Image
Examples
Embodiment 1
[0034] Such as figure 1 -Shown in 5, a kind of wide lead tape production line winding automatic control system of the present invention is arranged after the tape feeding device, comprises PLC control system and winding device, and winding device is used to receive the lead tape that feeding device sends into, The automatic control system of the wide lead strip production line also includes a buffer mechanism 1 arranged between the tape feeding device and the winding device. The buffer mechanism 1 includes an angle sensor 5, a cylinder 6, a first pallet, a second pallet and a pinch shaft 7 , the buffer mechanism 1 is triangular as a whole, the two supporting plates form the two sides of the triangle respectively, the cylinder 6 forms the third side of the triangle, the angle sensor 5 is arranged at the junction of the two supporting plates, the first supporting plate is fixed, The other end of the second pallet that the angle sensor 5 rotates is provided with a pinch shaft 7 f...
Embodiment 2
[0043] Such as Figure 6 As shown, the buffer mechanism 1 in this embodiment can be arranged between the roughing mill and the finishing mill in the rolling process. Due to the different rolling speeds of the roughing mill and the finishing mill, lead may be caused between the roughing mill and the finishing mill. In the case of strip 3 accumulation, by setting the buffer mechanism 1, the accumulation situation of lead strip 3 can be effectively monitored, and the PLC control system controls less accumulation, so that the tension of the rolled lead strip meets the product requirements. Other structures and control principles of this embodiment are the same as those of Embodiment 1.
[0044]
PUM
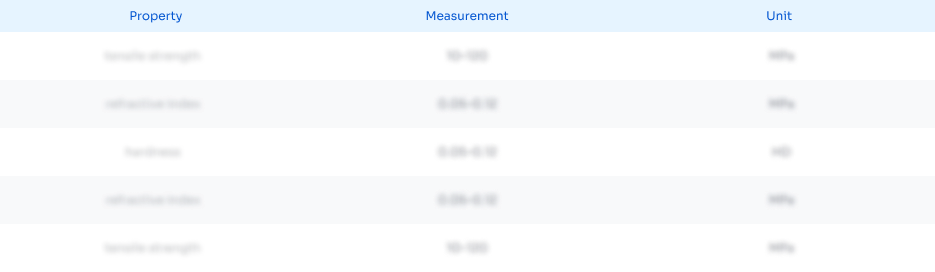
Abstract
Description
Claims
Application Information

- R&D Engineer
- R&D Manager
- IP Professional
- Industry Leading Data Capabilities
- Powerful AI technology
- Patent DNA Extraction
Browse by: Latest US Patents, China's latest patents, Technical Efficacy Thesaurus, Application Domain, Technology Topic, Popular Technical Reports.
© 2024 PatSnap. All rights reserved.Legal|Privacy policy|Modern Slavery Act Transparency Statement|Sitemap|About US| Contact US: help@patsnap.com