Composite method of composite BOPP film of art paper
A technology of coated paper and coated plate, which is applied in chemical instruments and methods, synthetic resin layered products, lamination devices, etc., can solve the problems of reducing production efficiency, affecting the quality of finished products, and increasing the cost of manufacturers, so as to improve production efficiency, The effect of reducing production cost and shortening production cycle
- Summary
- Abstract
- Description
- Claims
- Application Information
AI Technical Summary
Problems solved by technology
Method used
Examples
Embodiment 1
[0031] A kind of composite method of coated paper composite BOPP film comprises the following steps:
[0032] Adjust the room temperature of the production site to be 20°C and the humidity to be 45%.
[0033] (1) Install the BOPP film roll and coated paper roll on the compound machine;
[0034] (2) Inject the dry coating glue into the composite machine and start the heating system of the oven;
[0035] (3) When it reaches 40°C, start the transmission motor of the composite machine and start production;
[0036] (4) The anti-roll device pulls the BOPP film roll through the anilox roller, and performs drying treatment after gluing and coating;
[0037] (5) BOPP film rolls and coated paper rolls are bonded, the bonding temperature is 80°C, the bonding speed is 25 m / min, and the surface pressure during bonding is 120 kg / cm2.
Embodiment 2
[0039] A kind of composite method of coated paper composite BOPP film comprises the following steps:
[0040] Adjust the room temperature of the production site to be 25°C and the humidity to be 65%.
[0041] (1) Install the BOPP film roll and coated paper roll on the compound machine;
[0042] (2) Inject the dry coating glue into the composite machine and start the heating system of the oven;
[0043] (3) When it reaches 45°C, start the transmission motor of the composite machine and start production;
[0044] (4) The anti-roll device pulls the BOPP film roll through the anilox roller, and performs drying treatment after gluing and coating;
[0045] (5) BOPP film rolls and coated paper rolls are bonded, the bonding temperature is 85°C, the bonding speed is 35 m / min, and the surface pressure during bonding is 140 kg / cm2.
Embodiment 3
[0047] A kind of composite method of coated paper composite BOPP film comprises the following steps:
[0048] Adjust the room temperature of the production site to be 24°C and the humidity to be 55%.
[0049] (1) Install the BOPP film roll and coated paper roll on the compound machine;
[0050] (2) Inject the dry coating glue into the composite machine and start the heating system of the oven;
[0051] (3) When it reaches 42°C, start the transmission motor of the composite machine and start production;
[0052] (4) The anti-roll device pulls the BOPP film roll through the anilox roller, and performs drying treatment after gluing and coating;
[0053] (5) BOPP film rolls and coated paper rolls are bonded, the bonding temperature is 83°C, the bonding speed is 30 m / min, and the surface pressure during bonding is 135 kg / cm2.
[0054] The finished products of the above three embodiments have been tested, and the composite between the BOPP film and the coated paper is smooth and ...
PUM
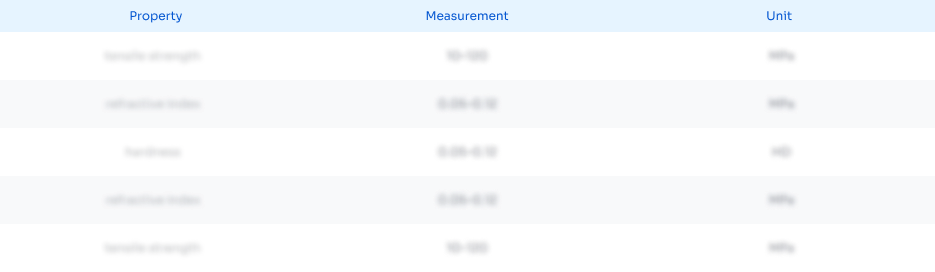
Abstract
Description
Claims
Application Information

- R&D Engineer
- R&D Manager
- IP Professional
- Industry Leading Data Capabilities
- Powerful AI technology
- Patent DNA Extraction
Browse by: Latest US Patents, China's latest patents, Technical Efficacy Thesaurus, Application Domain, Technology Topic, Popular Technical Reports.
© 2024 PatSnap. All rights reserved.Legal|Privacy policy|Modern Slavery Act Transparency Statement|Sitemap|About US| Contact US: help@patsnap.com