Welding repair method for local damage of G42CrMo4N cold rolling shaft sleeve
A welding repair and shaft sleeve technology, applied in the field of welding, can solve the problems of immature welding repair methods, affecting the smooth progress of production, affecting the safety of equipment use, etc., and achieves the effect of reducing the consumption of spare parts, easy to implement, and novel in concept.
- Summary
- Abstract
- Description
- Claims
- Application Information
AI Technical Summary
Problems solved by technology
Method used
Image
Examples
Embodiment Construction
[0034] The welding repair process for partial damage of G42CrMo4N cold-rolled bushing is: bushing surface cleaning --- surfacing surface processing --- making surfacing pad --- installing surfacing pad --- welding --- stress relief annealing ---Post-weld inspection---Return to the original size and finish machining, specifically follow the steps below:
[0035] 1. Clean the surface of the shaft sleeve.
[0036] Use hydrochloric acid to clean the surface of the shaft sleeve 1, and thoroughly clean the oil on the surface of the shaft sleeve; then use oxygen-propane flame heating and purge to clean the residual oil; finally, use an angle grinder to polish the metal luster in the welding repair area .
[0037] 2. Overlay welding surface processing.
[0038] Use an angle grinder to smooth the irregular fracture surface so that the deposited metal can be fully fused during surfacing.
[0039] 3. Make surfacing pad
[0040] Make a tubular liner that fits closely with the shaft sl...
PUM
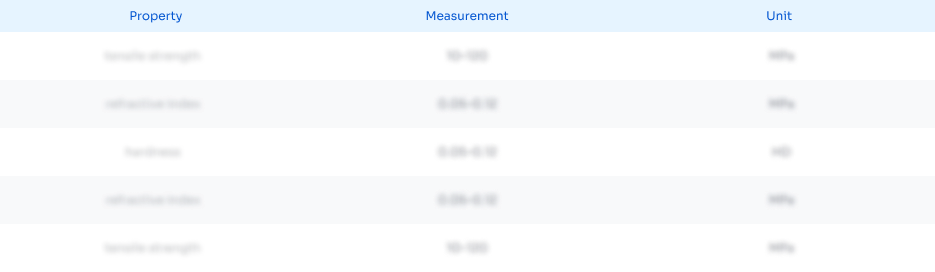
Abstract
Description
Claims
Application Information

- R&D Engineer
- R&D Manager
- IP Professional
- Industry Leading Data Capabilities
- Powerful AI technology
- Patent DNA Extraction
Browse by: Latest US Patents, China's latest patents, Technical Efficacy Thesaurus, Application Domain, Technology Topic, Popular Technical Reports.
© 2024 PatSnap. All rights reserved.Legal|Privacy policy|Modern Slavery Act Transparency Statement|Sitemap|About US| Contact US: help@patsnap.com