Copper precision part burr removal method
A technology for removing burrs and parts, applied in the field of machining, can solve problems affecting assembly quality, small size, low quality and low efficiency, etc., to improve surface finish and oxidation resistance, improve processing time, and high consistency Effect
- Summary
- Abstract
- Description
- Claims
- Application Information
AI Technical Summary
Problems solved by technology
Method used
Examples
Embodiment 1
[0014] After the copper precision parts are degreased and cleaned, rinse the workpiece, put the workpiece into the ultrasonic wave for 5 minutes, and then soak the large copper precision parts in the corrosion inhibitor solution for 15 minutes, heating and controlling the temperature at 45 degrees Celsius , the corrosion inhibitor formula is as follows:
[0015] Corrosion inhibitor formula (mass percentage): defoamer 0.3%, OP-7 emulsifier 0.3%, benzotriazole 0.5%, benzothiazole sodium salt 1%, 2,5-dimercaptothiadiazole disodium (30% aqueous solution) 10%, the rest is water.
[0016] After taking out the workpiece, put it directly into the corrosion solution preheated to 45 degrees Celsius, and ultrasonically corrode for 1 minute. The corrosion solution formula is as follows:
[0017] Corrosion solution formula 1 (mass percentage): ferric chloride 35%, hydrochloric acid 5%, defoamer 0.3%, OP-7 emulsifier 0.3%, benzotriazole 0.5%, mercaptobenzothiazole sodium salt 1%, The res...
Embodiment 2
[0019] After degreasing and cleaning the copper precision parts, rinse the workpiece, put the workpiece into the ultrasonic wave for 10 minutes, then soak the copper precision parts in the corrosion inhibitor solution for 15 minutes, heat and keep the temperature at 50 degrees Celsius, and slowly The formula of etching solution is as follows.
[0020] Corrosion inhibitor formula (mass percentage): defoamer 0.3%, OP-7 emulsifier, 0.5%, benzotriazole 0.5%, benzothiazole sodium salt 1%, 2,5-dimercaptothiadiazole Sodium (30% aqueous solution) 10%, the rest is water.
[0021] After taking out the workpiece, put it directly into the preheated 40°C corrosion solution, and ultrasonically corrode it for 2.5 minutes. The corrosion solution formula is as follows.
[0022] Corrosion solution formula (mass percentage): 8% ammonium chloride, 0.8% sodium chlorate, 25% concentrated hydrochloric acid, 0.3% defoamer, 0.3-0.5% OP-4 emulsifier, 0.5% benzotriazole, 2 , 5-dimercaptothiadiazole d...
Embodiment 3
[0024] After degreasing and cleaning the copper precision parts, rinse the workpiece, put the workpiece into the ultrasonic wave for 5 minutes, and then soak the copper precision parts in the corrosion inhibitor solution for 12.5 minutes, heat and control the temperature at 45 degrees Celsius to inhibit corrosion The liquid formula is as follows:
[0025] Corrosion inhibitor formula (mass percentage): defoamer 0.3%, OP-7 emulsifier, 0.3%, benzotriazole 0.5%, benzothiazole sodium salt 1%, 2,5-dimercaptothiadiazole Sodium (30% aqueous solution) 10%, the rest is water.
[0026] After taking out the workpiece, put it directly into the corrosion solution preheated to 45 degrees Celsius, and ultrasonically corrode for 4 minutes. The corrosion solution formula is as follows:
[0027] Corrosion solution formula 1 (mass percentage): ferric chloride 35%, hydrochloric acid 5%, defoamer 0.3%, OP-7 emulsifier 0.3%, benzotriazole 0.5%, mercaptobenzothiazole sodium salt 1%, The rest is wa...
PUM
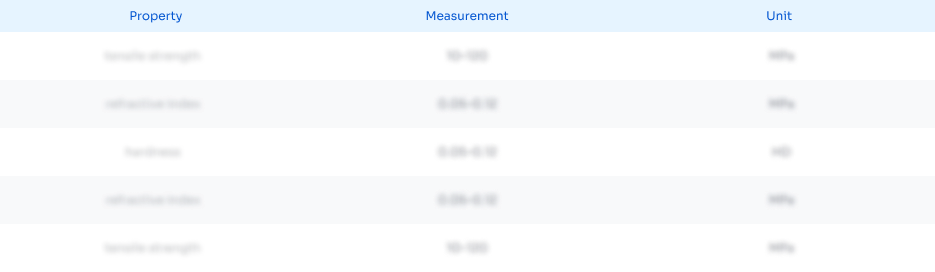
Abstract
Description
Claims
Application Information

- R&D Engineer
- R&D Manager
- IP Professional
- Industry Leading Data Capabilities
- Powerful AI technology
- Patent DNA Extraction
Browse by: Latest US Patents, China's latest patents, Technical Efficacy Thesaurus, Application Domain, Technology Topic, Popular Technical Reports.
© 2024 PatSnap. All rights reserved.Legal|Privacy policy|Modern Slavery Act Transparency Statement|Sitemap|About US| Contact US: help@patsnap.com