Blast furnace batching method based on final slag alkalinity
A technology of final slag basicity and blast furnace, which is applied in blast furnaces, blast furnace details, furnaces, etc., can solve problems such as increased blast furnace fuel consumption, increased influence of basicity, and reduced CaO content, and achieves stable blast furnace final slag basicity, Guarantee the effect of steady flow and simplify the adjustment
- Summary
- Abstract
- Description
- Claims
- Application Information
AI Technical Summary
Problems solved by technology
Method used
Examples
Embodiment Construction
[0010] The present invention will be further described below in conjunction with embodiment.
[0011] Embodiment raw fuel composition wt% is as table:
[0012] TF CaO Si0 2 S Sinter 56.20 9.55 4.90 0.012 Pellet 65.44 0.19 5.67 0.006 coke 0.00 0.00 6.50 0.750 pulverized coal 0.00 1.29 3.53 0.560
[0013] The total consumption of each batch of sinter and pellets is Y=100 tons, given that the basicity of the blast furnace slag is 1.12, the Si content of pig iron is 0.45%, the coke ratio into the furnace is 0.36t / t, and the coal ratio is 0.16t / t.
[0014] If the amount of sinter is X tons, the amount of pellets is (100-X) tons, and the theoretical production of molten iron per batch is: Fe 批 =0.995×[X×56.2%+(100-X)×65.44%] / 0.95. In the formula: 0.995 is the net iron content in molten iron; 0.95 is the iron content in molten iron.
[0015] According to the calculation formula of final slag basicity, final slag basicity = ...
PUM
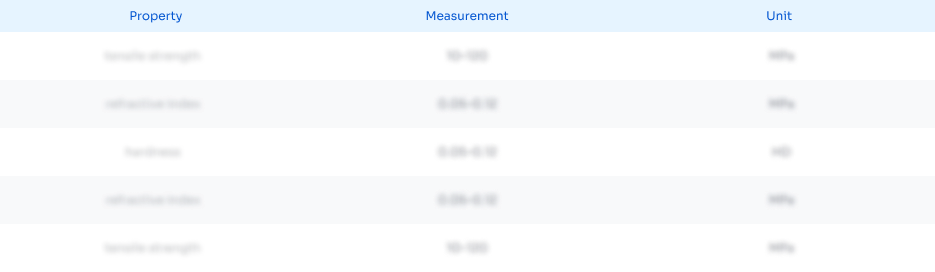
Abstract
Description
Claims
Application Information

- R&D
- Intellectual Property
- Life Sciences
- Materials
- Tech Scout
- Unparalleled Data Quality
- Higher Quality Content
- 60% Fewer Hallucinations
Browse by: Latest US Patents, China's latest patents, Technical Efficacy Thesaurus, Application Domain, Technology Topic, Popular Technical Reports.
© 2025 PatSnap. All rights reserved.Legal|Privacy policy|Modern Slavery Act Transparency Statement|Sitemap|About US| Contact US: help@patsnap.com