Method for treating waste carbide slag and waste hydrochloric acid
A technology of waste calcium carbide and waste hydrochloric acid, which is applied in chlorine/hydrogen chloride purification, calcium/strontium/barium halide, calcium/strontium/barium chloride, etc., to achieve effective comprehensive utilization, quality assurance, and good reaction effect
- Summary
- Abstract
- Description
- Claims
- Application Information
AI Technical Summary
Problems solved by technology
Method used
Image
Examples
Embodiment 1
[0023] Inject the waste calcium carbide slag and water into the activated carbon pretreatment device with a stirring device in a weight ratio of 1:1.8 and stir to form a uniform emulsion, settle naturally for 40 seconds, and send it to a filter press to obtain calcium hydroxide. The supernatant of the waste calcium carbide slag slurry is stored for later use; the waste hydrochloric acid is treated with activated carbon adsorption to obtain relatively pure hydrochloric acid. Take 400g of 25% hydrochloric acid in a 1000ml flask, slowly add 140g of carbide slag (calcium hydroxide) pretreated with activated carbon, dry and crushed, under stirring, control the reaction temperature at 90°C, and use 1% waste calcium carbide slag slurry as the supernatant liquid (calcium hydroxide solution) absorption. After the addition, the stirring reaction was continued until the pH value was 12, and then the stirring was stopped and filtered. Weigh 400g of filtrate, heat and concentrate on an el...
Embodiment 2
[0025] Inject the waste calcium carbide slag and water into the activated carbon pretreatment device with a stirring device in a weight ratio of 1:2 and stir to form a uniform emulsion, settle naturally for 50 seconds, and send it to a filter press to obtain calcium hydroxide. The supernatant of the waste calcium carbide slag slurry is stored for later use; the waste hydrochloric acid is treated with activated carbon adsorption to obtain relatively pure hydrochloric acid. Take 400g of 30% hydrochloric acid in a 1000ml flask, slowly add 150g of calcium carbide slag (calcium hydroxide) (water content 8%, dry basis calcium hydroxide content 80%, particle size less than 1mm) under stirring, add 3g of activated carbon simultaneously, and control the reaction temperature At 85°C, the generated waste gas is absorbed with 1% calcium hydroxide solution. After the addition, the stirring reaction was continued until the pH value was 12, and then the stirring was stopped and filtered. We...
Embodiment 3
[0027] Inject the waste calcium carbide slag and water into the activated carbon pretreatment device with a stirring device at a weight ratio of 1:2.2 and stir to form a uniform emulsion, settle naturally for 60 seconds, and send it to a filter press to obtain calcium hydroxide. The supernatant of the waste calcium carbide slag slurry is stored for later use; the waste hydrochloric acid is treated with activated carbon adsorption to obtain relatively pure hydrochloric acid. Take 300g of 30% hydrochloric acid in a 1000ml flask, slowly add 110g of calcium carbide slag (calcium hydroxide) (water content 8%, dry basis calcium hydroxide content 80%, particle size less than 1mm) under stirring, simultaneously add 3g of activated carbon, and control the reaction temperature At 80°C, the generated waste gas is absorbed with 1% calcium hydroxide solution. After the addition, the stirring reaction was continued until the pH value was 12, and then the stirring was stopped and filtered. ...
PUM
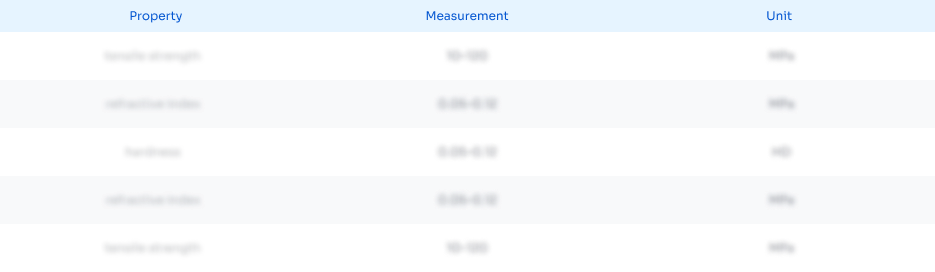
Abstract
Description
Claims
Application Information

- R&D Engineer
- R&D Manager
- IP Professional
- Industry Leading Data Capabilities
- Powerful AI technology
- Patent DNA Extraction
Browse by: Latest US Patents, China's latest patents, Technical Efficacy Thesaurus, Application Domain, Technology Topic, Popular Technical Reports.
© 2024 PatSnap. All rights reserved.Legal|Privacy policy|Modern Slavery Act Transparency Statement|Sitemap|About US| Contact US: help@patsnap.com