Automobile engine mounting bracket and manufacture method thereof
An automobile engine and mounting bracket technology, applied in the field of machinery, can solve problems such as easy cracking, uneven stress, and can not meet the needs of automobile technology development, and achieve the effect of large operating space, ensuring stability, and good design flexibility
- Summary
- Abstract
- Description
- Claims
- Application Information
AI Technical Summary
Problems solved by technology
Method used
Image
Examples
Embodiment Construction
[0018] The following is attached Figure 1~3 An embodiment of the invention is described:
[0019] Such as figure 1 and 2 As shown, the automobile engine suspension bracket includes a base 1, a support plate 2, a bracket 3, a mounting hole 4 and a suspension hole 5, and the support plate 2 has a curved portion 6, and the curved portion 6 is arranged on the support plate 2. In the middle, the bending angle is 12.5-16.5°;
[0020] The base 1, the support plate 2 and the support 3 are integrated, one end of the support plate 2 is connected to the base 1, and the other end is connected to the support 3. There are two corresponding hanging holes 5 on the support 3; Flange 7, the installation holes 4 are distributed on the base 1 in a triangular shape, and are located between the bracket 3 and the flange 7;
[0021] The base 1, the support plate 2 and the bracket 3 are made of steel material of SAPH400, and the thickness of the material is 3.5mm;
[0022] Such as image 3 As s...
PUM
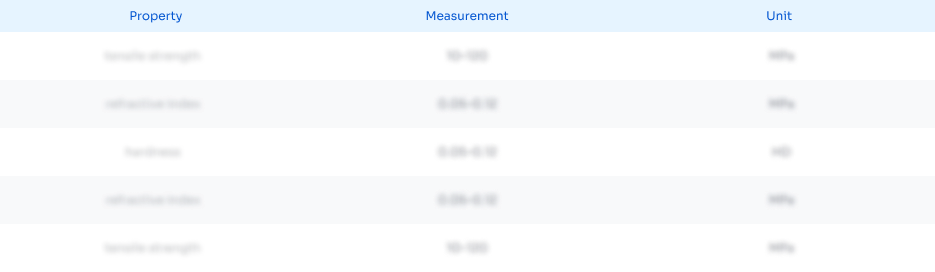
Abstract
Description
Claims
Application Information

- Generate Ideas
- Intellectual Property
- Life Sciences
- Materials
- Tech Scout
- Unparalleled Data Quality
- Higher Quality Content
- 60% Fewer Hallucinations
Browse by: Latest US Patents, China's latest patents, Technical Efficacy Thesaurus, Application Domain, Technology Topic, Popular Technical Reports.
© 2025 PatSnap. All rights reserved.Legal|Privacy policy|Modern Slavery Act Transparency Statement|Sitemap|About US| Contact US: help@patsnap.com