Light anti-slipping high-wear-resistance rubber material for sole and preparation method thereof
A rubber material, high wear-resistant technology, applied in the field of rubber composite materials, can solve the problems of inability to meet strenuous exercise, poor shock absorption, heavy quality, etc.
- Summary
- Abstract
- Description
- Claims
- Application Information
AI Technical Summary
Problems solved by technology
Method used
Image
Examples
Embodiment 1
[0044] The formula of this embodiment is as follows (note: each raw material is by weight)
[0045] EVA: 65
[0046] NR: 15
[0047] SBR: 15
[0048] CaCO3:4
[0049] Si-69 wear agent: 4
[0050] ZnO: 3
[0051] ZnST: 3
[0052] ST: 1.5
[0053] DCP: 1
[0054] AC: 1.8.
[0055] The preparation method is as follows:
[0056] First mix other raw materials except DCP and AC for banburying, add DCP and AC 5 minutes before the end of banburying, granulate after the end of banburying, and then one-time injection molding to obtain the light weight non-slip and high wear-resistant rubber Material.
[0057] During banburying, control temperature is 125 ℃, banburying time is 18min.
[0058] During one injection molding, the control temperature is 185°C and the time is 4min.
Embodiment 2
[0060] The formula of this embodiment is as follows (note: each raw material is by weight):
[0061] EVA: 60
[0062] NR: 10
[0063] SBR: 20
[0064] CaCO3:5
[0065] AG-209 wear agent: 3
[0066] ZnO: 2
[0067] ZnST: 4
[0068] ST: 2
[0069] DCP: 0.8
[0070] AC: 1.5.
[0071] The preparation method is as follows:
[0072] First mix other raw materials except DCP and AC for banburying, add DCP and AC 4 minutes before the end of banburying, granulate after the end of banburying, and then make the above-mentioned light weight non-slip and high wear-resistant rubber by one injection molding Material.
[0073] During banburying, control temperature is 120 ℃, banburying time is 20min.
[0074] During one injection molding, the temperature is controlled at 180°C and the time is 5 minutes.
Embodiment 3
[0076] The formula of this embodiment is as follows (note: each raw material is by weight):
[0077] EVA: 70
[0078] NR: 20
[0079] SBR: 10
[0080] CaCO3:3
[0081] Si-69 wear agent: 5
[0082] ZnO: 4
[0083] ZnST: 2
[0084] ST: 1
[0085] DCP: 1.2
[0086] AC: 2.
[0087] The preparation method is as follows:
[0088] First mix other raw materials except DCP and AC for banburying, add DCP and AC 6 minutes before the end of banburying, granulate after banburying, and then make the above-mentioned light weight non-slip and high wear-resistant rubber by one injection molding Material.
[0089] During banburying, control temperature is 135 ℃, banburying time is 12min.
[0090] During one-time injection molding, the temperature is controlled at 195°C and the time is 3 minutes.
PUM
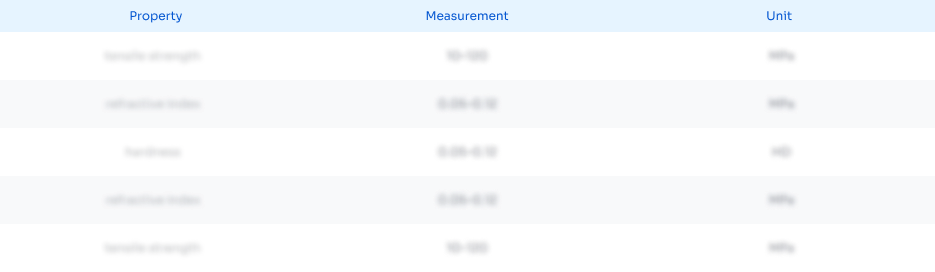
Abstract
Description
Claims
Application Information

- R&D Engineer
- R&D Manager
- IP Professional
- Industry Leading Data Capabilities
- Powerful AI technology
- Patent DNA Extraction
Browse by: Latest US Patents, China's latest patents, Technical Efficacy Thesaurus, Application Domain, Technology Topic, Popular Technical Reports.
© 2024 PatSnap. All rights reserved.Legal|Privacy policy|Modern Slavery Act Transparency Statement|Sitemap|About US| Contact US: help@patsnap.com