Powder recovery separator of power station boiler
A power plant boiler and separator technology, which is applied in grain processing and other fields, can solve problems such as the influence of coal mill output, and achieve the effect of novel structure and remarkable energy saving effect
- Summary
- Abstract
- Description
- Claims
- Application Information
AI Technical Summary
Problems solved by technology
Method used
Image
Examples
Embodiment Construction
[0008] The upper part of the main body 1 is fixedly connected to the air lock 2, and inside the main body is fixedly connected to an impact cone 3 with a "?"-shaped cross section. The cross section of the impact cone is an equilateral triangle. The body below the impact cone has an air inlet 4 , There is a qualified powder outlet 5 that opens diagonally upward on the body above the impact cone, a partition 6 is fixedly connected to the inner wall of the body below the impact cone, and a discharge port 7 is provided below the body.
[0009] The air and powder mixture coming out of the outlet of the coal mill enters the body from the two air locks set above, so that the coal particles hit the impact cone and then bend back. It is a kind of parabolic motion. The wind entering from the air inlet blows upward, making The qualified powder is led out from the qualified powder outlet; the medium-sized coal powder enters the channel formed by the partition and the body under the action of ...
PUM
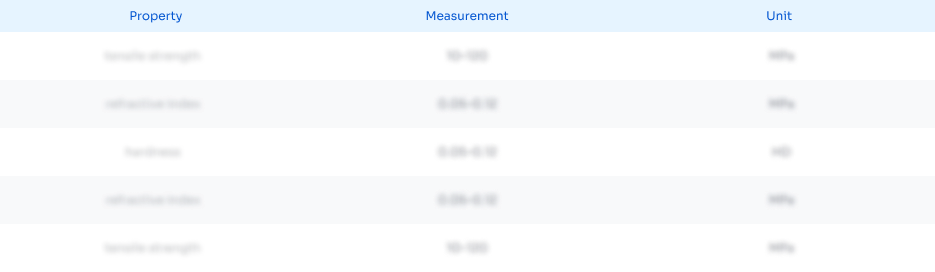
Abstract
Description
Claims
Application Information

- Generate Ideas
- Intellectual Property
- Life Sciences
- Materials
- Tech Scout
- Unparalleled Data Quality
- Higher Quality Content
- 60% Fewer Hallucinations
Browse by: Latest US Patents, China's latest patents, Technical Efficacy Thesaurus, Application Domain, Technology Topic, Popular Technical Reports.
© 2025 PatSnap. All rights reserved.Legal|Privacy policy|Modern Slavery Act Transparency Statement|Sitemap|About US| Contact US: help@patsnap.com