Warm extrusion forming process of stylus printing head base and forming mould thereof
A needle-type printing head and forming process technology, which is applied in the direction of metal extrusion dies, etc., to achieve the effects of convenient operation, reduced energy consumption, and easy forming
- Summary
- Abstract
- Description
- Claims
- Application Information
AI Technical Summary
Problems solved by technology
Method used
Image
Examples
Embodiment Construction
[0031] specific implementation plan
[0032] The present invention will be further described in detail below in conjunction with the embodiments and accompanying drawings.
[0033] The utility model relates to a forming mold for the warm extrusion forming process of a needle print head base, which includes a warm extrusion mold and a blanking mold.
[0034] refer to figure 1, the warm extrusion die includes an upper mold base A1, a lower mold base A17, a punch assembly A, a die assembly, an ejection assembly, a guide post A11, and a guide post A11 matched. Set A 5, the guide post A 11 and the guide sleeve A 5 arranged between the upper die base A 1 and the lower die base A 17 play a role in guiding and positioning; the punch assembly A includes a punch A 3, punch fixing plate A 4, punch backing plate A 2, the punch A 3 is engaged in the punch fixing plate A 4, the connector screws and vertical pins pass through the upper die base A 1, the punch Die backing plate A 2, punch ...
PUM
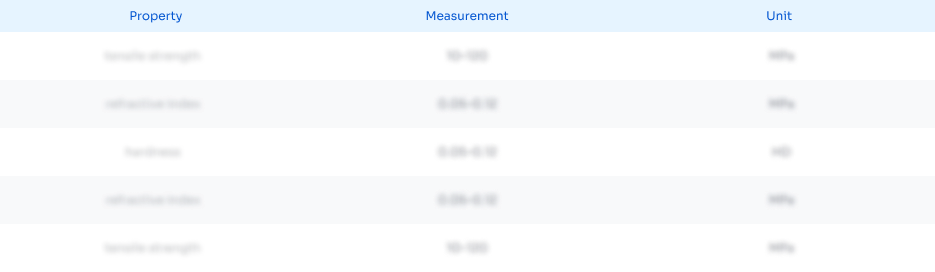
Abstract
Description
Claims
Application Information

- R&D
- Intellectual Property
- Life Sciences
- Materials
- Tech Scout
- Unparalleled Data Quality
- Higher Quality Content
- 60% Fewer Hallucinations
Browse by: Latest US Patents, China's latest patents, Technical Efficacy Thesaurus, Application Domain, Technology Topic, Popular Technical Reports.
© 2025 PatSnap. All rights reserved.Legal|Privacy policy|Modern Slavery Act Transparency Statement|Sitemap|About US| Contact US: help@patsnap.com