Exhaust heat recovery device of textile printing and dyeing forming machine
A waste heat recovery device, textile printing and dyeing technology, applied in the direction of heat exchanger types, indirect heat exchangers, fixed conduit components, etc., can solve problems such as air pollution, increased production costs of enterprises, energy loss, etc., to extend the contact time, prolong Traveling distance and the effect of improving heat exchange efficiency
- Summary
- Abstract
- Description
- Claims
- Application Information
AI Technical Summary
Problems solved by technology
Method used
Image
Examples
Embodiment Construction
[0017] The present invention will be described in further detail below through specific examples.
[0018] like figure 1 As shown, a recovery device for exhaust gas waste heat of a textile printing and dyeing setting machine, a recovery pool 1, the recovery pool 1 is equipped with an air washing heat transfer fluid, the bottom of the recovery pool 1 is provided with an exhaust gas inlet 10, and the top is provided with an exhaust gas outlet 2, the recovery pool 1 1 is provided with a coil, one end of the coil protrudes from the recovery tank 1 to form a water inlet 11, and the other end protrudes from the recovery tank 1 to form a water outlet 4, the waste gas inlet 10 is connected to the intake pipeline, and the waste gas outlet 2 is connected to the Gas line, the bottom of recovery tank 1 is provided with drain port 9, and this drain port 9 can also be used as liquid filling port, certainly, also can open another liquid filling port on recovery tank 1.
[0019] Wherein, the...
PUM
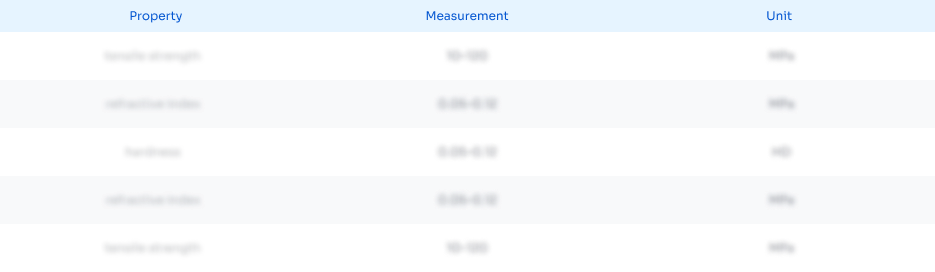
Abstract
Description
Claims
Application Information

- R&D
- Intellectual Property
- Life Sciences
- Materials
- Tech Scout
- Unparalleled Data Quality
- Higher Quality Content
- 60% Fewer Hallucinations
Browse by: Latest US Patents, China's latest patents, Technical Efficacy Thesaurus, Application Domain, Technology Topic, Popular Technical Reports.
© 2025 PatSnap. All rights reserved.Legal|Privacy policy|Modern Slavery Act Transparency Statement|Sitemap|About US| Contact US: help@patsnap.com