Mixed calcined cement admixture being produced through utilizing papermaking white mud, shale and coal gangue
A paper-making white mud and mixed material technology, which is applied in the field of Portland cement, can solve the problems of non-wood pulp paper-making white mud industrialization without precedent, occupying large land resources, and difficult to promote economic benefits.
- Summary
- Abstract
- Description
- Claims
- Application Information
AI Technical Summary
Problems solved by technology
Method used
Examples
Embodiment 1
[0013] Example 1 According to the chemical composition analysis of white mud, shale, and coal gangue and the measurement results of the calorific value of coal gangue, the Ca / Si molar ratio is 1.2 as the ratio of white mud and shale, and the coal gangue is 30% of the total mass. % for batching, mixing evenly and aging for 24 hours, the moisture content is 11.5%, then the mixture is molded under the pressure of 3-5MPa, dried for 6 hours, and then heated up to 1000℃ in the high temperature furnace at a heating rate of 5℃ / min , and keep it warm for 30 minutes, and then rapidly cool to ambient temperature to make a composite material. According to the requirements of GB / T12957-2005 "Industrial Waste Residue Activity Test Method for Cement Admixtures", grind the admixture in a small test mill for about 30 minutes, and grind until the sieve residue of 80 μm square hole is 1-3%. The mixed material is mixed into Portland cement at a ratio of 30%, and then mixed with 5% gypsum to make ...
Embodiment 2
[0014] Example 2 According to the chemical composition analysis of lime mud, shale, and coal gangue and the calorific value measurement results of coal gangue, the Ca / Si molar ratio is 1.6 as the ratio of white mud and shale, and coal gangue is 30% of the total mass. % for batching, mixing evenly and aging for 24 hours, the moisture content is 13.3%, and then the mixture is molded under the pressure of 3-5MPa, dried for 6 hours and then heated to 1000℃ in the high temperature furnace at a heating rate of 5℃ / min , and keep it warm for 30 minutes, and then rapidly cool to ambient temperature to make a composite material. According to the requirements of GB / T12957-2005 "Industrial Waste Residue Activity Test Method for Cement Admixtures", grind the admixture in a small test mill for about 30 minutes, and grind until the sieve residue of 80 μm square hole is 1-3%. The mixed material is mixed into Portland cement at a ratio of 30%, and then mixed with 5% gypsum to make a sample. T...
Embodiment 3
[0015] Example 3 According to the chemical composition analysis of lime mud, shale and coal gangue and the calorific value measurement results of coal gangue, the Ca / Si molar ratio is 2.0 as the ratio of white mud and shale, and the coal gangue is 30% of the total mass. % for batching, mixing evenly and aging for 24 hours, the moisture content is 14.4%, then the mixture is molded under the pressure of 3-5MPa, dried for 6 hours, and then heated to 1000℃ in the high temperature furnace at a heating rate of 5℃ / min , and keep it warm for 30 minutes, and then rapidly cool to ambient temperature to make a composite material. According to the requirements of GB / T12957-2005 "Industrial Waste Residue Activity Test Method for Cement Admixtures", grind the admixture in a small test mill for about 30 minutes, and grind until the sieve residue of 80 μm square hole is 1-3%. The mixed material is mixed into Portland cement at a ratio of 30%, and then mixed with 5% gypsum to make a sample. T...
PUM
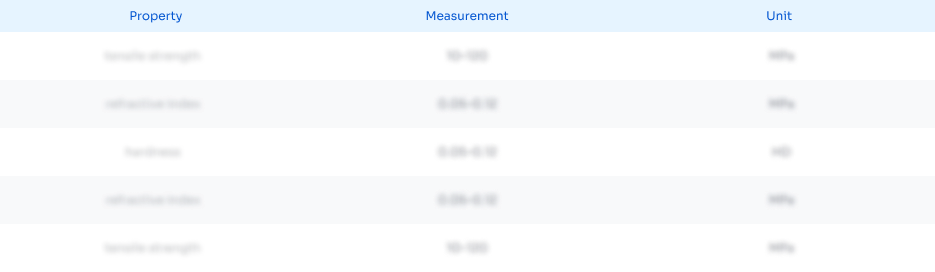
Abstract
Description
Claims
Application Information

- R&D
- Intellectual Property
- Life Sciences
- Materials
- Tech Scout
- Unparalleled Data Quality
- Higher Quality Content
- 60% Fewer Hallucinations
Browse by: Latest US Patents, China's latest patents, Technical Efficacy Thesaurus, Application Domain, Technology Topic, Popular Technical Reports.
© 2025 PatSnap. All rights reserved.Legal|Privacy policy|Modern Slavery Act Transparency Statement|Sitemap|About US| Contact US: help@patsnap.com