Method and device for improving formability of tailor-welded steel plate
A formability and steel plate technology, applied in heat treatment equipment, furnaces, heat treatment furnaces, etc., can solve the problems of product dimensional accuracy decline, energy waste, metal oxidation, etc., achieve the effect of less energy consumption, less energy consumption, and improved formability
- Summary
- Abstract
- Description
- Claims
- Application Information
AI Technical Summary
Problems solved by technology
Method used
Image
Examples
Embodiment 1
[0023] The method in the present invention is applied to equal-thickness laser-welded steel plates whose parent material is No. 45 high-quality carbon structural steel. The No. 45 high-quality carbon structural steel is water-quenched at 860°C and tempered at 180°C with a thickness of 1.0mm.
[0024] 1) According to the ferromagnetic properties of No. 45 steel plate and the welding direction, determine the reasonable magnetic treatment process parameters: the magnetic induction intensity of the low-frequency alternating magnetic field is 1.5T~1.7T, to ensure that the base metal of the tailor-welded steel plate reaches the magnetic saturation state, and the magnetic field frequency is 0.2 Hz~2Hz, the magnetic treatment time is 260s~300s, and the magnetic treatment direction is perpendicular to the weld seam.
[0025] 2) Place the tailor-welded steel plate in a low-frequency alternating magnetic field, and perform magnetic field stress relief treatment on it according to the abov...
Embodiment 2
[0029] The method of the present invention is applied to the equal-thickness laser welded steel plate whose base material is 30CrMnMoTiA. The thickness of 30CrMnMoTiA is 0.75mm after oil quenching at 875°C and tempering at 440°C.
[0030] 1) According to the ferromagnetic properties of 30CrMnMoTiA steel plate and the welding direction, determine the reasonable magnetic treatment process parameters: the magnetic induction intensity is 1.8T~2.0T, to ensure that the base metal of tailor welded steel plate reaches the magnetic saturation state, the magnetic field frequency is 7Hz~10Hz, and the magnetic treatment time It is 120s~180s, and the direction of magnetic treatment is the direction perpendicular to the weld seam.
[0031] 2) Place the tailor-welded steel plate in a low-frequency alternating magnetic field, and perform magnetic field stress relief treatment on it according to the above-mentioned magnetic treatment process parameters.
[0032] 3) Take out the tailor-welded s...
Embodiment 3
[0035] The method in the present invention is applied to the laser tailor welded steel plate whose parent material is DX56D+Z hot-rolled galvanized steel and DP600 hot-rolled dual-phase steel. DX56D+Z hot-rolled galvanized steel and DP600 hot-rolled dual-phase steel have been treated with stress relief annealing at 500°C, and the thickness is 0.75mm.
[0036] 1) According to the ferromagnetic properties and welding direction of DX56D+Z steel plate and DP600 steel plate, reasonable magnetic treatment process parameters are determined: the magnetic induction intensity is 2.0T~2.2T, which ensures that the base materials of the two tailor-welded steel plates reach magnetic saturation; the magnetic field frequency 2Hz~5Hz, the magnetic treatment time is 40s~80s, and the magnetic treatment direction is perpendicular to the weld seam.
[0037] 2) Place the tailor-welded steel plate in a low-frequency alternating magnetic field, and perform magnetic field stress relief treatment on it...
PUM
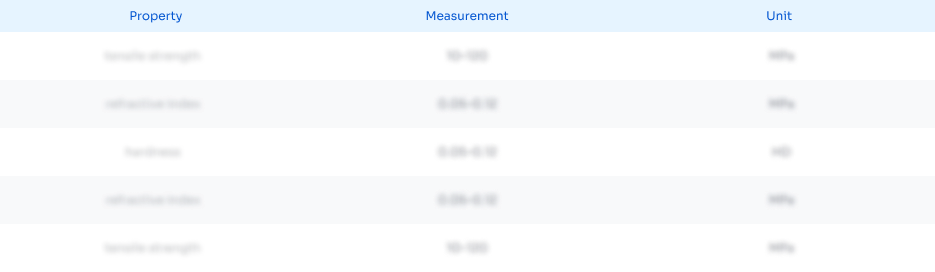
Abstract
Description
Claims
Application Information

- R&D
- Intellectual Property
- Life Sciences
- Materials
- Tech Scout
- Unparalleled Data Quality
- Higher Quality Content
- 60% Fewer Hallucinations
Browse by: Latest US Patents, China's latest patents, Technical Efficacy Thesaurus, Application Domain, Technology Topic, Popular Technical Reports.
© 2025 PatSnap. All rights reserved.Legal|Privacy policy|Modern Slavery Act Transparency Statement|Sitemap|About US| Contact US: help@patsnap.com