Pretreatment method for silylation and silylation method comprising same
A monosilane and pretreatment technology, which is applied in the manufacture of electrical components, semiconductor/solid-state devices, circuits, etc., can solve problems such as peeling, particles in the layer, and failure of resist patterns, and achieve the effect of improving product yield
- Summary
- Abstract
- Description
- Claims
- Application Information
AI Technical Summary
Problems solved by technology
Method used
Image
Examples
Embodiment 1
[0027] The system for silylation includes: a heating system, a processing chamber, a silylating agent input port, a nitrogen gas input port, an exhaust port, a vacuum system, and a control module.
[0028] Turn on the heating system, control the constant temperature of the processing chamber at 125°C, put the wafer to be processed into the processing chamber, blow in nitrogen, and control the flow rate to 10,000 milliliters / minute (ml / min). After 10s, the mixed gas of HMDS and nitrogen is introduced. The volume ratio of HMDS and nitrogen is: 45:55. After the control flow is 15s, the mixed gas is stopped and the nitrogen is continued. The control flow is 2000 ml / min (ml / min ), and exhaust from the exhaust port.
[0029] The whole process is controlled by the control module, and the processing chamber temperature is kept constant during the process. After the pretreatment, the wafers were subjected to a general silylation treatment, and the obtained wafers were subjected to a c...
PUM
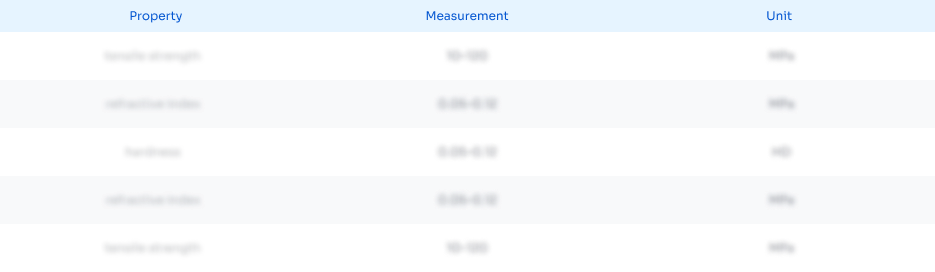
Abstract
Description
Claims
Application Information

- R&D
- Intellectual Property
- Life Sciences
- Materials
- Tech Scout
- Unparalleled Data Quality
- Higher Quality Content
- 60% Fewer Hallucinations
Browse by: Latest US Patents, China's latest patents, Technical Efficacy Thesaurus, Application Domain, Technology Topic, Popular Technical Reports.
© 2025 PatSnap. All rights reserved.Legal|Privacy policy|Modern Slavery Act Transparency Statement|Sitemap|About US| Contact US: help@patsnap.com