Inside engaged gear pump or gear motor device with multilayer structure
A technology of internal meshing gear pumps and gear motors, applied to pumps, rotary piston pumps, rotary or swinging piston engines, etc., can solve the problems of manufacturing difficulty and manufacturing cost, increased internal leakage of the device, and failure of device functions, etc., to achieve Reduce processing difficulty and manufacturing cost, improve contact sealing state, and prolong service life
- Summary
- Abstract
- Description
- Claims
- Application Information
AI Technical Summary
Problems solved by technology
Method used
Image
Examples
Embodiment 1
[0034] Embodiment 1 (n=1)
[0035] see figure 2 a to figure 2 As shown in f, in Embodiment 1 of the present invention, the multi-layer internal gear pump includes a shaft 1, an inner rotor 2, a double-sided toothed ring sleeve 3, an outer rotor 4, a pump body 5, a rear cover 6 and The front cover 7; the number of teeth of the inner and outer rotors and the double-sided toothed ring sleeve is equal to 1; in this embodiment, the number of teeth of the inner rotor 2 is 1 less than that of the double-sided toothed ring sleeve 3, and the number of teeth of the double-sided toothed ring sleeve 3 is less than that of the outer rotor 4. The number of teeth is less 1; the tooth profile of the inner rotor 2, the double-sided toothed ring sleeve 3 and the outer rotor 4 adopts a cycloid tooth profile design. In this embodiment, the numbers of teeth of the inner rotor 2 , the double-sided toothed collar 3 and the outer rotor 4 are 4, 5, and 6, respectively.
[0036] In this embodiment...
Embodiment 2
[0037] Embodiment 2 (n>1)
[0038] see image 3 As shown, in Embodiment 2 of the present invention, the internal meshing gear pump of this multi-layer structure includes a shaft 1, an inner rotor 2, a double-sided toothed ring sleeve 3, an outer rotor 4, a pump body 5, a rear cover 6, a front Cover 7, the first crescent partition 8 and the second crescent partition 9; the difference between the number of teeth of the inner and outer rotors and the double-sided tooth ring sleeve 3 is greater than 1 (also known as the multi-tooth difference structure); in this embodiment, the inner rotor 2 The number of teeth of the double-sided toothed collar 3 is 4 less than that of the double-sided toothed collar 3, and the number of teeth of the double-sided toothed collar 3 is 4 less than that of the outer rotor 4; Open profile, cycloid profile or other profile designs. In this embodiment, the numbers of teeth of the inner rotor 2 , the double-sided toothed collar 3 and the outer rotor 4 ...
Embodiment 3
[0041] see Figure 4 As shown, in the third embodiment of the present invention, the difference between the internal gear pump with multi-layer structure and the first embodiment is that the difference in the number of teeth between the inner rotor 2 and the toothed collar 3 is equal to 1, and the outer rotor 4 The difference between the number of teeth and the toothed ring sleeve 3 is greater than 1; the inner rotor 2, the double-sided toothed ring sleeve 3 and the outer rotor 4 can adopt cycloid tooth profile design, and the structural part with a tooth difference greater than 1 can also use involute teeth outline design. In this embodiment, the numbers of teeth of the inner rotor 2 , the double-sided toothed collar 3 and the outer rotor 4 are 4, 5, and 8, respectively. According to the third scheme, the inner rotor 2, the double-sided toothed ring sleeve 3, the crescent partition 8 and the outer rotor 4 are installed in the pump body 5 from the inside to the outside in seq...
PUM
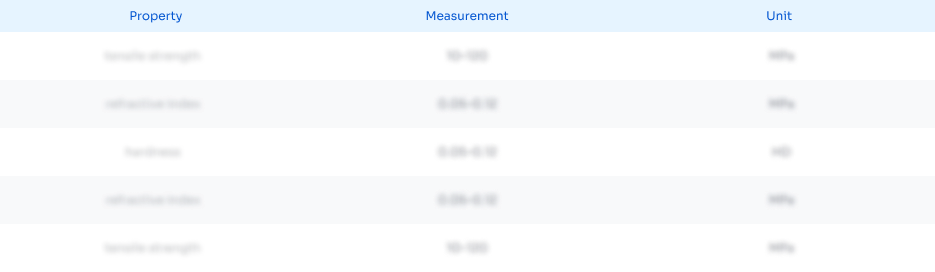
Abstract
Description
Claims
Application Information

- R&D
- Intellectual Property
- Life Sciences
- Materials
- Tech Scout
- Unparalleled Data Quality
- Higher Quality Content
- 60% Fewer Hallucinations
Browse by: Latest US Patents, China's latest patents, Technical Efficacy Thesaurus, Application Domain, Technology Topic, Popular Technical Reports.
© 2025 PatSnap. All rights reserved.Legal|Privacy policy|Modern Slavery Act Transparency Statement|Sitemap|About US| Contact US: help@patsnap.com