Method for preparing surface-coated anode material of lithium battery
A positive electrode material and surface coating technology, applied in the field of battery positive electrode material preparation, can solve the problems of poor high-temperature storage performance, low capacity, and poor cycle performance, and achieve good cycle stability, high-quality specific capacity, cycle good stability effect
- Summary
- Abstract
- Description
- Claims
- Application Information
AI Technical Summary
Problems solved by technology
Method used
Examples
Embodiment 1
[0019] Blend and heat treat
[0020] Put the positive electrode materials lithium iron phosphate, lithium nickel cobaltate, magnesium nitrate, and cobalt oxide in a mixing and drying kettle with a mass ratio of 30:5:10:10, start the mixer to mix to form a mixture, and the obtained mixture After being heated to above the melting point of magnesium nitrate and reacting for 2 hours, cool down for subsequent use.
[0021] Hydrolysis reaction
[0022] Ball mill the cooled mixture and pass through a 100-mesh sieve, then place it in a mixing and drying kettle, place a saturated lithium hydroxide solution accounting for 1% by mass of the mixture in a spray system, and control the spray system to Spray, mix for 1 hour after spraying, so that the saturated solution of lithium hydroxide is evenly adsorbed on the surface of the mixture, continue to start the mixer, and place the aluminum sulfate whose content is just completely reacted with lithium hydroxide in the spray system, and ...
Embodiment 2
[0028] Blend and heat treat
[0029] Place the positive electrode materials lithium iron phosphate, lithium nickel cobaltate, magnesium nitrate, and cobalt oxide in a mixing and drying kettle with a mass ratio of 40:10:15:20, start the mixer to mix, and form a mixture. After being heated to above the melting point of magnesium nitrate and reacting for 6 hours, cool down for subsequent use.
[0030] Hydrolysis reaction
[0031] Ball mill the cooled mixture, pass through a 200-mesh sieve, and then place it in a mixing and drying kettle. Put a saturated solution of lithium hydroxide accounting for 2% of the mixture in the spray system, and control the spray system to the mixing and drying kettle. Spray, mix for 3 hours after spraying, so that the saturated solution of lithium hydroxide is evenly adsorbed on the surface of the mixture, continue to start the mixer, and place the aluminum sulfate whose content is just completely reacted with lithium hydroxide in the spray syste...
PUM
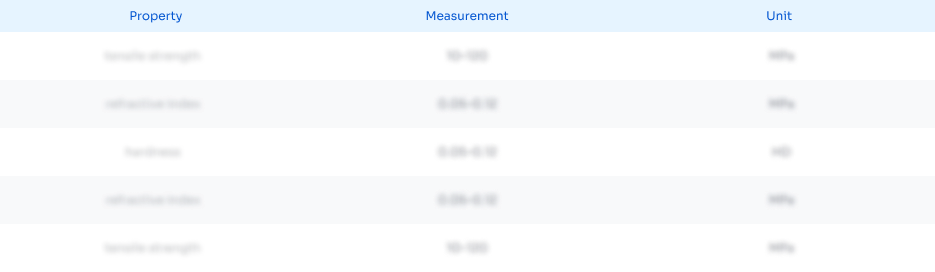
Abstract
Description
Claims
Application Information

- R&D
- Intellectual Property
- Life Sciences
- Materials
- Tech Scout
- Unparalleled Data Quality
- Higher Quality Content
- 60% Fewer Hallucinations
Browse by: Latest US Patents, China's latest patents, Technical Efficacy Thesaurus, Application Domain, Technology Topic, Popular Technical Reports.
© 2025 PatSnap. All rights reserved.Legal|Privacy policy|Modern Slavery Act Transparency Statement|Sitemap|About US| Contact US: help@patsnap.com