Production method of glassine body paper
A technology of glassine base paper and production method, which is applied in papermaking, textiles and papermaking, fiber raw material processing, etc., which can solve the problems of low transparency of glassine base paper, high transparency of glassine base paper, and lower internal strength, etc., and achieve low surface Oil absorption value, high tensile strength, high transparency effect
- Summary
- Abstract
- Description
- Claims
- Application Information
AI Technical Summary
Problems solved by technology
Method used
Examples
Embodiment 1
[0022] Embodiment 1: adopt 100% bleached kraft softwood pulp, after beating and refining, pulp degree is controlled at 45 ○ SR, and add 0.2% (weight) of sizing agent to mix, go through the headbox online copying, pressing, and pre-drying section, the moisture is controlled at 3%, add starch and use the film transfer sizing machine for surface sizing, sizing The amount is 1.5g / m 2 , into the post-drying section, the moisture is controlled at 5%, and is humidified by a humidifier with a spray humidification system. The spray volume is 7%, and the moisture reaches 12% after spraying; and then calendered by a super calender 3 calendering zones, each consisting of a soft roll and a hard roll, with a pressure of 300 kN / m 2 , roll surface temperature 300 ○ C; The proportions listed above are relative to the total amount of pulp;
Embodiment 2
[0023] Embodiment 2: adopt 100% bleached kraft softwood pulp, after beating and refining, pulp degree is controlled at 50 ○ SR, and add 0.4% (weight) of sizing agent for mixing. After going through the headbox online copying, pressing, and pre-drying section, the moisture is controlled at 6%, and polyvinyl alcohol is added to carry out surface sizing through a film transfer sizing machine. The amount of sizing is 0.5g / m 2 , into the post-drying section, the moisture is controlled at 8%, and it is wetted by a humidifier with a spray humidification system. The spray volume is 8%, and the moisture reaches 16% after spraying; and then calendered by a super calender 6 calendering zones, each consisting of a soft roll and a hard roll, with a pressure of 200 kN / m 2 , roll surface temperature 100 ○ C; The proportions listed above are relative to the total amount of pulp;
Embodiment 3
[0024] Embodiment 3: adopt 100% bleached kraft softwood pulp, after beating and refining, pulp degree is controlled at 40 ○ SR, and add 0.07% (weight) of sizing agent for mixing, after going through the headbox online copying, pressing, and pre-drying section, the water content is controlled at 4%, adding starch and passing the film transfer sizing machine for surface sizing, sizing The amount is 3g / m 2 , into the post-drying section, the moisture is controlled at 6%, and it is humidified through a humidifier with a spray humidification system. The spray volume is 8%, and the moisture reaches 14% after spraying; and then calendered by a super calender 5 calendering zones, each consisting of a soft roll and a hard roll, with a pressure of 400 kN / m 2 , roll surface temperature 250 ○ C; The proportions listed above are relative to the total amount of pulp;
[0025] After the above-described embodiment is completed, the slitting package is wound up at last.
PUM
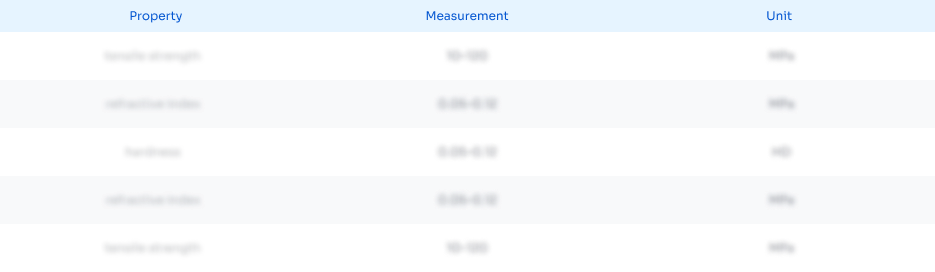
Abstract
Description
Claims
Application Information

- R&D Engineer
- R&D Manager
- IP Professional
- Industry Leading Data Capabilities
- Powerful AI technology
- Patent DNA Extraction
Browse by: Latest US Patents, China's latest patents, Technical Efficacy Thesaurus, Application Domain, Technology Topic, Popular Technical Reports.
© 2024 PatSnap. All rights reserved.Legal|Privacy policy|Modern Slavery Act Transparency Statement|Sitemap|About US| Contact US: help@patsnap.com