Ladle bottom casting method and lashed area reinforced castable construction mould thereof
A castable and bottom pouring technology, which is applied in the direction of manufacturing tools, metal processing equipment, casting melt containers, etc., can solve the problems of steel leakage at the bottom of the ladle, resistance to erosion, corrosion, etc., and achieve enhanced resistance to molten steel erosion and extended length , The effect of facilitating construction
- Summary
- Abstract
- Description
- Claims
- Application Information
AI Technical Summary
Problems solved by technology
Method used
Image
Examples
Embodiment Construction
[0018] The present invention will be further described in detail below in conjunction with the accompanying drawings and specific embodiments.
[0019] figure 2 The castable construction mold shown in the impact zone includes a U-shaped frame 1, and the U-shaped frame 1 is surrounded by two parallel long frames 1.1 and one short frame 1.2. The height of the U-shaped frame 1 is equal to the thickness of the impact brick 4 . An opening 1.3 that can surround the impact brick 4 is formed between the ends of two parallel long frames 1.1, two support plates 2 are arranged between the tops of the two long frames 1.1, and the tops of the long frame 1.1 and the short frame 1.2 are A plurality of hooks 3 are provided.
[0020] Ladle bottom pouring method of the present invention comprises the following steps:
[0021] 1) Before pouring, such as figure 1 As shown, first place the impact brick 4, nozzle seat brick 6 and two breathable bricks 7 in the impact area to the corresponding ...
PUM
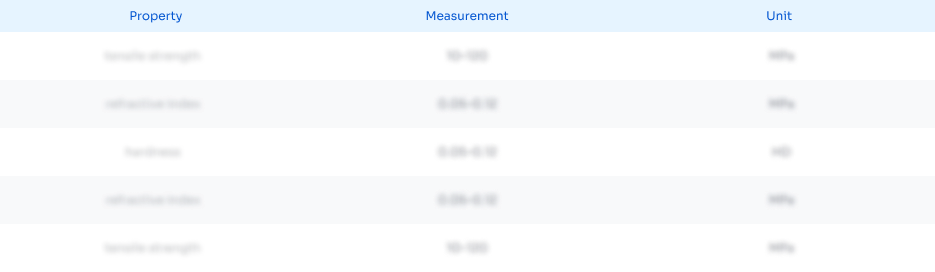
Abstract
Description
Claims
Application Information

- R&D
- Intellectual Property
- Life Sciences
- Materials
- Tech Scout
- Unparalleled Data Quality
- Higher Quality Content
- 60% Fewer Hallucinations
Browse by: Latest US Patents, China's latest patents, Technical Efficacy Thesaurus, Application Domain, Technology Topic, Popular Technical Reports.
© 2025 PatSnap. All rights reserved.Legal|Privacy policy|Modern Slavery Act Transparency Statement|Sitemap|About US| Contact US: help@patsnap.com