Cast steel node manufacturing process
A production process and steel casting node technology, applied in the control of molten metal pouring from the casting ladle, casting mold, casting mold composition, etc., can solve the problem that welding residual stress cannot be eliminated, material utilization rate is not high, and deformation is difficult to predict and other problems, to achieve the effect of convenient on-site construction and installation, good spatial angle consistency, and convenient operation
- Summary
- Abstract
- Description
- Claims
- Application Information
AI Technical Summary
Problems solved by technology
Method used
Image
Examples
Embodiment 1
[0013] A production process of cast steel node. The main components of the node are calculated by weight percentage, C=0.2~0.3, Si=0.6~0.8, Mn=1.1~1.3, P≤0.035, S≤0.01, Cu≤0.3, it It includes the following steps:
[0014] S1. Furnace charge equipment and molten metal smelting. The charge includes scrap steel, pouring risers, waste castings, steel scraps and pig iron, using electric arc furnace three-phase alkaline electric arc furnace, smelting by oxidation, and finally deoxidizing under white slag;
[0015] S2. Modeling process, using the α-set modeling method to select alkali phenolic resin, curing agent, and sand modeling. The resin addition is 1.7% of the sand weight, and the curing agent is 20% of the resin weight. Sand, curing agent, and resin are used. Stir and mix in sequence;
[0016] S3. Pouring process. Single injection hole bottom pouring ladle is used for pouring, horizontal pouring and horizontal cooling are used. During pouring, the inner casting surface rises at a sp...
Embodiment 2
[0025] A production process of cast steel node. The main components of the node are calculated by weight percentage, C=0.2~0.3, Si=0.6~0.8, Mn=1.1~1.3, P≤0.035, S≤0.01, Cu≤0.3, it It includes the following steps:
[0026] S1. Furnace charge equipment and molten metal smelting. The charge includes scrap steel, pouring risers, waste castings, steel scraps and pig iron, using electric arc furnace three-phase alkaline electric arc furnace, smelting by oxidation, and finally deoxidizing under white slag;
[0027] S2. Modeling process. Alkali phenolic resin, curing agent and sand are selected by the α-set modelling method. The resin addition is 1% of the sand weight, and the curing agent is 15% of the resin weight. Sand, curing agent, and resin are used. Stir and mix in sequence;
[0028] S3. Pouring process. Single injection hole bottom pouring ladle is used for pouring, horizontal pouring and horizontal cooling are used. During pouring, the inner casting surface rises at a speed of 12mm...
Embodiment 3
[0037] A production process of cast steel node. The main components of the node are calculated by weight percentage, C=0.2~0.3, Si=0.6~0.8, Mn=1.1~1.3, P≤0.035, S≤0.01, Cu≤0.3, it It includes the following steps:
[0038] S1. Furnace charge equipment and molten metal smelting. The charge includes scrap steel, pouring risers, waste castings, steel scraps and pig iron, using electric arc furnace three-phase alkaline electric arc furnace, smelting by oxidation, and finally deoxidizing under white slag;
[0039] S2. Modeling process, using the α-set modeling method to select alkali phenolic resin, curing agent, and sand modeling. The resin addition is 2% of the sand weight, and the curing agent is 25% of the resin weight. Sand, curing agent, and resin are used. Stir and mix in sequence;
[0040] S3. Pouring process. Single injection hole bottom pouring ladle is used for pouring, horizontal pouring and horizontal cooling are used. During pouring, the inner casting surface rises at a spee...
PUM
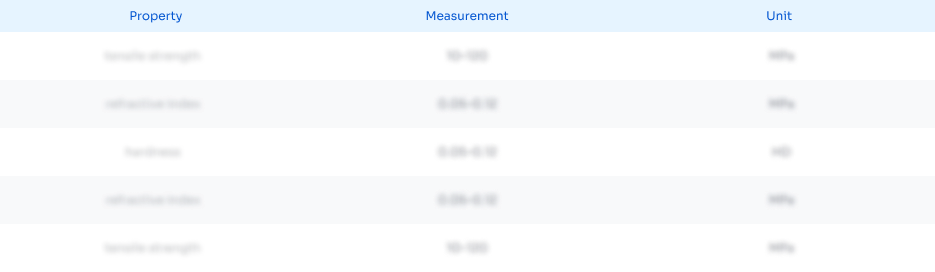
Abstract
Description
Claims
Application Information

- Generate Ideas
- Intellectual Property
- Life Sciences
- Materials
- Tech Scout
- Unparalleled Data Quality
- Higher Quality Content
- 60% Fewer Hallucinations
Browse by: Latest US Patents, China's latest patents, Technical Efficacy Thesaurus, Application Domain, Technology Topic, Popular Technical Reports.
© 2025 PatSnap. All rights reserved.Legal|Privacy policy|Modern Slavery Act Transparency Statement|Sitemap|About US| Contact US: help@patsnap.com