Special chamfering device for self-fastening stator core
A technology of stator iron core and chamfering device, applied in the direction of manufacturing stator/rotor body, etc., can solve the problems of inconvenient processing, low efficiency and high production cost
- Summary
- Abstract
- Description
- Claims
- Application Information
AI Technical Summary
Problems solved by technology
Method used
Image
Examples
Embodiment Construction
[0017] See attached figure 1 , The self-locking stator core special chamfering device disclosed in the present invention includes a press-fit mechanism for press-fitting both ends of the stator core 1, a chamfering knife assembly 3, and a driving chamfering knife assembly 3 close to or away from the stator iron The displacement driving mechanism 4 at the outer circle of one end of the core 1 and the rotation driving mechanism 5 driving the chamfering knife assembly 3 to rotate around the outer circle of one end of the stator core 1 to chamfer the outer circle of the stator core 1. By adopting the above technical solution, when the stator core 1 is chamfered, the stator core 1 is first press-fitted by the press-fitting mechanism 2, and then the chamfering knife assembly 3 is driven close to one end of the stator core 1 by the displacement driving mechanism 4 The outer circle position, and finally the chamfering knife assembly 3 is driven to rotate around the outer circle of one e...
PUM
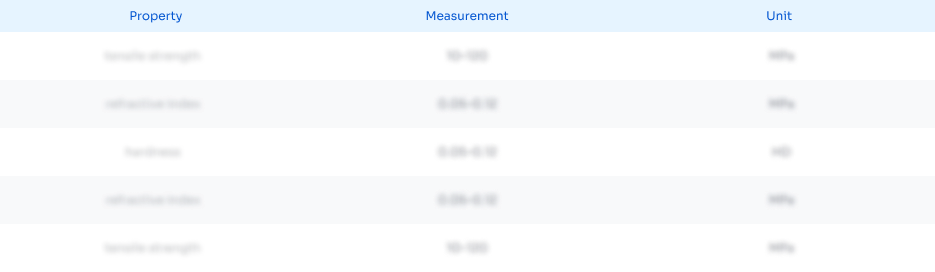
Abstract
Description
Claims
Application Information

- R&D
- Intellectual Property
- Life Sciences
- Materials
- Tech Scout
- Unparalleled Data Quality
- Higher Quality Content
- 60% Fewer Hallucinations
Browse by: Latest US Patents, China's latest patents, Technical Efficacy Thesaurus, Application Domain, Technology Topic, Popular Technical Reports.
© 2025 PatSnap. All rights reserved.Legal|Privacy policy|Modern Slavery Act Transparency Statement|Sitemap|About US| Contact US: help@patsnap.com