Constant speed servo unit for controlling angle signals and control method thereof
An angle signal and servo device technology, applied in the direction of the starting device for steering, can solve the problem of unbalanced steering speed and other problems, achieve long operating life, realize long-distance signal transmission, and have a strong ability to judge transmission faults Effect
- Summary
- Abstract
- Description
- Claims
- Application Information
AI Technical Summary
Problems solved by technology
Method used
Image
Examples
Embodiment Construction
[0016] Such as figure 1 As shown, the constant-speed rudder steering servo device controlled by an angle signal, the rudder steering column 6 is rotatably supported on the flange, the lower part of the rudder column 6 is fixed with the lower gear box 7, and the upper part of the rudder column 6 is installed with a large rotary gear 5. The rudder hydraulic motor 2 is fixed on the flange, the output shaft of the rudder hydraulic motor 2 is drivingly connected with the input shaft of the planetary reducer 3, and the output shaft of the planetary reducer 3 is installed with the driving pinion 4, which is connected to the rotary gear Gear 5 is meshed, such as figure 2 As shown, the rotary gear 5 is also meshed with the reduction gear 8, and the reduction gear 8 is provided with a rotary encoder 9, and the rotary encoder is an R36 series Hall encoder, preferably an R36A analog Hall encoder. The rotary encoder 9 communicates with the rudder angle indicator 11 and the PLC control un...
PUM
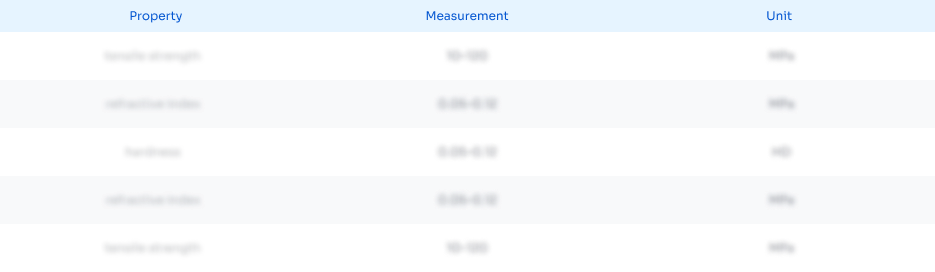
Abstract
Description
Claims
Application Information

- R&D
- Intellectual Property
- Life Sciences
- Materials
- Tech Scout
- Unparalleled Data Quality
- Higher Quality Content
- 60% Fewer Hallucinations
Browse by: Latest US Patents, China's latest patents, Technical Efficacy Thesaurus, Application Domain, Technology Topic, Popular Technical Reports.
© 2025 PatSnap. All rights reserved.Legal|Privacy policy|Modern Slavery Act Transparency Statement|Sitemap|About US| Contact US: help@patsnap.com