Built-in keel composite wood and its preparation method
A technology of inner keel and wood, which is applied in the field of built-in keel composite wood and its preparation, which can solve the problems of difficulty in confirming the grade of wood, achieve good insulation, overcome natural defects, and reduce materials
- Summary
- Abstract
- Description
- Claims
- Application Information
AI Technical Summary
Problems solved by technology
Method used
Image
Examples
Embodiment 1
[0021] The built-in keel composite wood of the present invention is composed of an outer layer board 1, an inner keel layer board 2 and a foamed polyurethane 3, and more than one layer of inner keel layer boards 2 arranged at intervals in the warp and weft direction are built between the two outer layer boards 1. The foamed polyurethane 3 is filled in the inner gap. The outer layer board 1 is composed of more than one wooden boards connected with each other by mortise and tenon in sequence. 2-5 layers of inner keel laminates 2 are built between the two outer layers 1 . The gap between the two outer skin boards 1 and the inner keel board 2 is formed by solidified foamed polyurethane 3 .
[0022] Its preparation method is as follows:
[0023] a. Material selection, surface cleaning, and processing into profile planks of uniform specifications;
[0024] b. Inserting the profile planks made in step a into the mold side by side to form the outer layer board 1;
[0025] c. Place...
Embodiment 2
[0032] The built-in keel composite wood of the present invention is composed of an outer layer board 1, an inner keel layer board 2 and a foamed polyurethane 3, and more than one layer of inner keel layer boards 2 arranged at intervals in the warp and weft direction are built between the two outer layer boards 1. The foamed polyurethane 3 is filled in the inner gap. The outer layer board 1 is composed of more than one wooden boards connected with each other by mortise and tenon in sequence. Three layers of inner keel laminates 2 are built between the two outer panels 1 . The gap between the two outer skin boards 1 and the inner keel board 2 is formed by solidified foamed polyurethane 3 .
[0033] Its preparation method is as follows:
[0034] a. Select suitable wood, clean the surface, and process it into profile planks of uniform specifications;
[0035] b. Arrange the profile planks prepared in step a side by side, and arrange them side by side with mortise and tenon join...
Embodiment 3
[0042] The built-in keel composite wood of the present invention is between the two outer layer boards 1, three layers of inner keel laminates are arranged at intervals in the warp direction, two layers of inner keel laminates 2 are arranged at intervals in the direction of latitude, and the inner keel in the direction of warp and weft Laminates are arranged alternately, filled with foamed polyurethane, and bonded to form a load-bearing, heat-insulating, air-insulating, and sound-insulating building material. The cross-sectional size of the board is determined according to the structural design, and the surface material is determined according to the architectural design. The thickness is 60-240, the width is 900-1500, and the length is 3000-8000. Among them, the inner keel is designed according to the bearing capacity requirements of the wall panel, and the surface plate is designed according to the decoration requirements; the surface plate and inner keel are designed accordi...
PUM
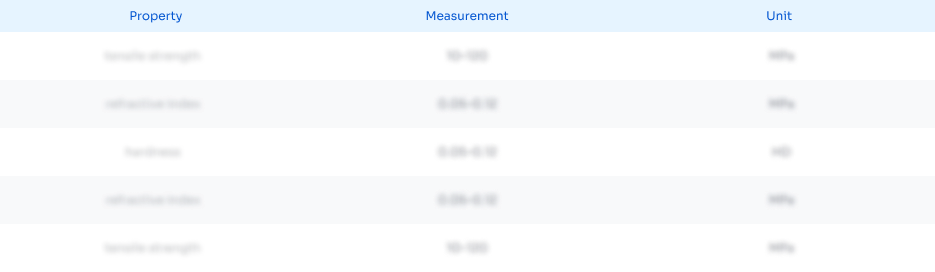
Abstract
Description
Claims
Application Information

- R&D Engineer
- R&D Manager
- IP Professional
- Industry Leading Data Capabilities
- Powerful AI technology
- Patent DNA Extraction
Browse by: Latest US Patents, China's latest patents, Technical Efficacy Thesaurus, Application Domain, Technology Topic, Popular Technical Reports.
© 2024 PatSnap. All rights reserved.Legal|Privacy policy|Modern Slavery Act Transparency Statement|Sitemap|About US| Contact US: help@patsnap.com