Conducting primer for electrostatic coating of plastic base material and preparation method thereof
An electrostatic coating and substrate technology, used in conductive coatings, coatings, polyester coatings, etc., can solve the problem of inability to meet the requirements of single-component primers for canning and recycling, poor water resistance, heat resistance, heat shock resistance, and inability to Applicable to PP plastic parts and other problems, to achieve the effect of excellent matching, good adhesion, and excellent thermal shock resistance
- Summary
- Abstract
- Description
- Claims
- Application Information
AI Technical Summary
Problems solved by technology
Method used
Image
Examples
Embodiment 1
[0046] The conductive primer for electrostatic coating of plastic substrates of the present embodiment is made up of the following components by weight: thermoplastic acrylic resin (Deqian resin AC-7435) 6kg, polyester resin (modified hydrophobicity shown in table 1) Polyester resin A1) 8kg, epoxy resin (Wuxi Di Aisheng 850S) 0.8kg, mixed solvent 50kg (wherein containing toluene 25kg, xylene 10kg, methyl isobutyl ketone 15kg), pigment dispersant 0.42kg (Bike Chemical Disperbyk 161 is 0.12kg, Lubrizol SOLSPERSE hyperdispersant 32500 is 0.24kg, Lubrizol SOLSPERSE hyperdispersant 5000 is 0.06kg), rutile titanium dioxide pigment (U.S. DuPont R-706 titanium dioxide) 5kg, conductive carbon Black pigment (Evonik Degussa Printex XE2-B conductive carbon black) 1kg, fumed silica (Degosa-Hess AEROSILR972) 1kg, polyolefin resin (polyurethane modified chlorinated polyolefin resin shown in Table 2 B1) 15kg, leveling agent (organic silicon leveling agent, Shin-Etsu Chemical KP-327) 0.001kg, ...
Embodiment 2
[0054] The conductive primer for electrostatic coating of plastic substrates of this embodiment consists of the following components by weight: thermoplastic acrylic resin (Deqian resin AC-7435) 8kg, polyester resin (modified hydrophobicity shown in Table 1) Polyester resin A2) 10kg, epoxy resin (Wuxi Diaisheng 850S) 0.8kg, mixed solvent 52kg (including toluene 25kg, xylene 12kg, methyl isobutyl ketone 15kg), pigment dispersant 0.42kg (byk chemical Disperbyk 161 is 0.12kg, Lubrizol SOLSPERSE hyperdispersant 32500 is 0.24kg, Lubrizol SOLSPERSE hyperdispersant 5000 is 0.06kg), rutile titanium dioxide pigment (Kemeiji CR826) 5kg, conductive carbon black pigment (win Chuang Degussa Printex XE2-B conductive carbon black) 1kg, fumed silica (Degosa-Hess AEROSIL R972) 1kg, polyolefin resin (polyurethane modified chlorinated polyolefin resin B1 shown in Table 2) 11kg , leveling agent (Shin-Etsu Chemical KP-327) 0.001kg, defoamer (Japan Kusei Chemical OX-70) 0.01kg, high boiling point a...
Embodiment 3
[0062] The conductive primer for electrostatic coating of plastic substrates of the present embodiment is made up of the following components by weight: thermoplastic acrylic resin (Nengda Chemical AC2080M) 6kg, polyester resin (modified hydrophobic polyester shown in Table 1) Resin A1) 8kg, epoxy resin (Wuxi Diaisheng 850S) 0.8kg, mixed solvent 52kg (including toluene 25kg, xylene 12kg, methyl isobutyl ketone 15kg), pigment dispersant 0.42kg (Bick chemical Disperbyk 161 0.12kg, Lubrizol SOLSPERSE hyperdispersant 32500 is 0.24kg, Lubrizol SOLSPERSE hyperdispersant 5000 is 0.06kg), rutile titanium dioxide pigment (U.S. DuPont R-706 titanium dioxide) 5kg, conductive carbon black (card Bote VXC72R) 3kg, fumed silica (Di Gaosha-Hess AEROSIL R972) 1kg, polyolefin resin (polyurethane modified chlorinated polyolefin resin B2 shown in Table 2) 13kg, leveling agent (Shin-Etsu Chemical KP -327) 0.001kg, defoamer (Japan Kusei Kasei OX-70) 0.01kg, high boiling point aromatic hydrocarbon s...
PUM
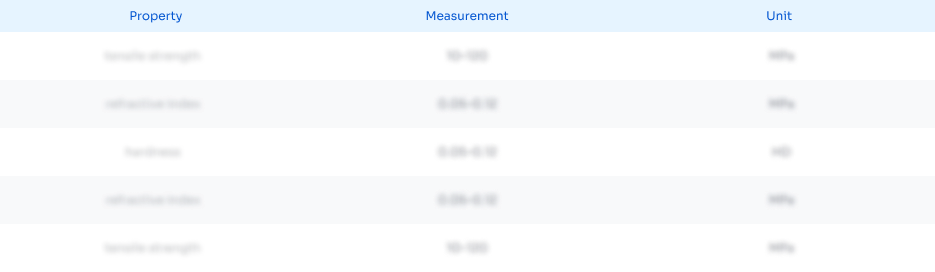
Abstract
Description
Claims
Application Information

- R&D Engineer
- R&D Manager
- IP Professional
- Industry Leading Data Capabilities
- Powerful AI technology
- Patent DNA Extraction
Browse by: Latest US Patents, China's latest patents, Technical Efficacy Thesaurus, Application Domain, Technology Topic, Popular Technical Reports.
© 2024 PatSnap. All rights reserved.Legal|Privacy policy|Modern Slavery Act Transparency Statement|Sitemap|About US| Contact US: help@patsnap.com