Shipment method combining large constructional element rolling and floating crane
A roll-on and component technology, applied in the directions of transportation, packaging, loading/unloading, etc., can solve the problems of difficulty in loading, high cost, and singleness, and achieve the effects of reducing construction costs, ensuring safe loading, and easy operation
- Summary
- Abstract
- Description
- Claims
- Application Information
AI Technical Summary
Problems solved by technology
Method used
Image
Examples
Embodiment 1
[0013] Embodiment 1 A ship loading method combining roll-off and floating cranes for large components, the steps are as follows:
[0014] (1) Shipping preparation: dock the special girder ship on wharf 3, on which pier 3 is overlapped with trestle 2, set up pier 1 in front of wharf 3, and place the stern on pier 1 in front of wharf 3; Components are transported to wharf 3 with two large flatbed trucks, and inspected before shipment;
[0015] (2) Ro-Ro ships and floating cranes are in place: choose the appropriate tide level. When the ship is at a tide level of 2m, the deck is flush with the wharf; The flatbed truck boarded and disembarked smoothly;
[0016] Anchor positioning according to the pre-designed position; along the transverse direction of the coastline, two parallel lap platforms are arranged on the special beam carrier, and two rows of parallel tracks are laid between the lap platforms;
[0017] (3) Component ro-ro boarding: the special-purpose large flatbed truck...
Embodiment 2
[0019] Embodiment 2 A method for combining large components with ro-ro and floating cranes, the steps are as follows:
[0020] (1) Shipping preparation: dock the special girder ship on wharf 3, on which pier 3 is overlapped with trestle 2, set up pier 1 in front of wharf 3, and place the stern on pier 1 in front of wharf 3; Components are transported to wharf 3 with two large flatbed trucks, and inspected before shipment;
[0021] (2) Ro-Ro ships and floating cranes are in place: choose the appropriate tide level. When the ship is at a tide level of 3m, the deck is flush with the wharf; The flatbed truck boarded and disembarked smoothly;
[0022] Anchor positioning according to the pre-designed position; along the transverse direction of the coastline, two parallel lap platforms are arranged on the special beam carrier, and two rows of parallel tracks are laid between the lap platforms;
[0023] (3) Component ro-ro boarding: the special-purpose large flatbed truck loaded wit...
Embodiment 3
[0025] Embodiment 3 A ship loading method combining roll-off and floating cranes for large components, the steps are as follows:
[0026] (1) Shipping preparation: dock the special girder ship on wharf 3, on which pier 3 is overlapped with trestle 2, set up pier 1 in front of wharf 3, and place the stern on pier 1 in front of wharf 3; Components are transported to wharf 3 with two large flatbed trucks, and inspected before shipment;
[0027] (2) Ro-Ro ships and floating cranes in place: choose the appropriate tide level. When the ship is at a tide level of 2.63m, the deck is flush with the wharf; The large flatbed truck boarded and disembarked smoothly;
[0028] Anchor positioning according to the pre-designed position; along the transverse direction of the coastline, two parallel lap platforms are arranged on the special beam carrier, and two rows of parallel tracks are laid between the lap platforms;
[0029] (3) Component ro-ro boarding: the special-purpose large flatbed ...
PUM
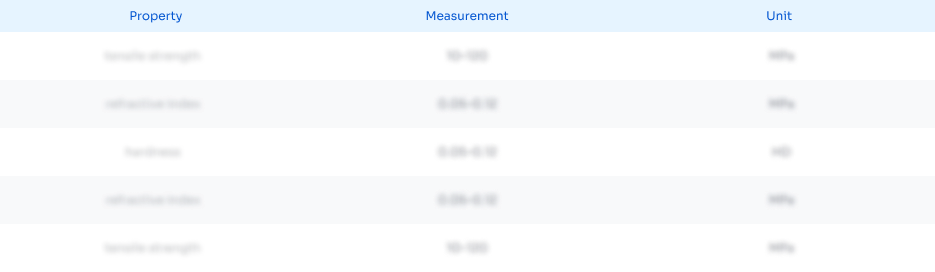
Abstract
Description
Claims
Application Information

- R&D Engineer
- R&D Manager
- IP Professional
- Industry Leading Data Capabilities
- Powerful AI technology
- Patent DNA Extraction
Browse by: Latest US Patents, China's latest patents, Technical Efficacy Thesaurus, Application Domain, Technology Topic, Popular Technical Reports.
© 2024 PatSnap. All rights reserved.Legal|Privacy policy|Modern Slavery Act Transparency Statement|Sitemap|About US| Contact US: help@patsnap.com