Desulfuration and impurity removal device and process of tunnel kiln exhaust gas
A tunnel kiln and waste gas technology, applied in waste heat treatment, furnace types, furnaces, etc., can solve the problems of poor absorption of sulfur dioxide or smoke, low desulfurization and dust removal efficiency, easy vaporization of lime water, etc., and achieves small footprint and reasonable design. , the effect of reducing pollution
- Summary
- Abstract
- Description
- Claims
- Application Information
AI Technical Summary
Problems solved by technology
Method used
Image
Examples
Embodiment 1
[0030] Such as Figure 1 to Figure 3 As shown, a desulfurization and impurity removal device for tunnel kiln exhaust gas in this embodiment includes a direct-fired tunnel 1, and the direct-fired tunnel 1 includes a drying zone 9 and a high-temperature firing zone 10 arranged in sequence. The direct firing tunnel 1 also includes a drying buffer zone 6, a waste gas collection channel 7 and a brick net, the drying buffer zone 6 is arranged in front of the drying zone 9, and the drying buffer zone 6 and the waste gas The collection channel 7 is connected, the brick net is set in the direct-fired tunnel 1, the desulfurization and impurity removal device also includes a side air channel 2, an air channel opening 3 and a ventilation gate 4, and the side air channel 2 is opened in the Inside the kiln walls on both sides of the direct firing tunnel 1, the top of the side air duct 2 is provided with an air gate 5, the air gate 4 is movably arranged on the air gate 5, and the air duct 3 ...
Embodiment 2
[0038] The difference between this embodiment and Embodiment 1 is that: the brick network in this embodiment also includes a first bridge 13, and the first bridge 13 is horizontally laid on the top of the brick row, and the first bridge 13 is A brick, the brick network also includes a second bridge 14, the second bridge 14 is arranged between the 7th and the 8th layer brick network layer, and the second bridge 14 is two bricks placed in parallel piece. The first bridge 13 at the top of the brick column is used to stabilize the brick column and reduce the gap, and the second bridge 14 can firmly support the brick layer stacked on the second bridge 14, so that the structure of the brick column is more stable, and then the brick network is ensured. Filtering effect.
[0039] Other structures of this embodiment are the same as those of Embodiment 1, and will not be repeated here.
PUM
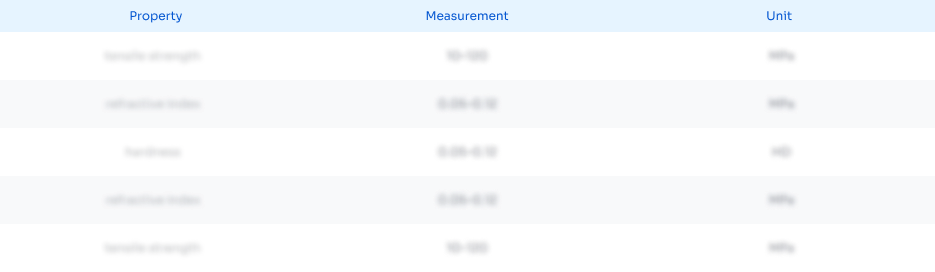
Abstract
Description
Claims
Application Information

- R&D
- Intellectual Property
- Life Sciences
- Materials
- Tech Scout
- Unparalleled Data Quality
- Higher Quality Content
- 60% Fewer Hallucinations
Browse by: Latest US Patents, China's latest patents, Technical Efficacy Thesaurus, Application Domain, Technology Topic, Popular Technical Reports.
© 2025 PatSnap. All rights reserved.Legal|Privacy policy|Modern Slavery Act Transparency Statement|Sitemap|About US| Contact US: help@patsnap.com