Strain design based economical pipe line steel and its manufacturing method
A technology for pipeline steel and manufacturing methods, applied in the direction of temperature control, etc., can solve the problems of extending rolling time, reducing production efficiency, and low rolling temperature, so as to improve rolling efficiency, reduce production cost, and reduce relaxation time Effect
- Summary
- Abstract
- Description
- Claims
- Application Information
AI Technical Summary
Problems solved by technology
Method used
Image
Examples
Embodiment Construction
[0035] The present invention will be further described below by way of examples.
[0036] The chemical composition (wt%) of the steel of the embodiment of the present invention is shown in Table 1, 1-14 in the table is the embodiment of the present invention, and 15-18 is the comparative example.
[0037] Table 1 The chemical composition of the embodiment steel of the present invention
[0038]
C
Si
mn
P
S
Ti
Nb
V
Cu
Ni
Cr
Mo
Al
1
0.06
0.30
1.70
0.01
0.003
0.017
0.03
0
0.22
0.23
0.20
0
0.04
2
0.06
0.25
1.65
0.01
0.003
0.012
0.04
0
0.15
0.17
0.16
0
0.03
3
0.07
0.40
1.60
0.01
0.003
0.015
0.03
0
0
0.40
0.11
0
0.03
4
0.07
0.35
...
PUM
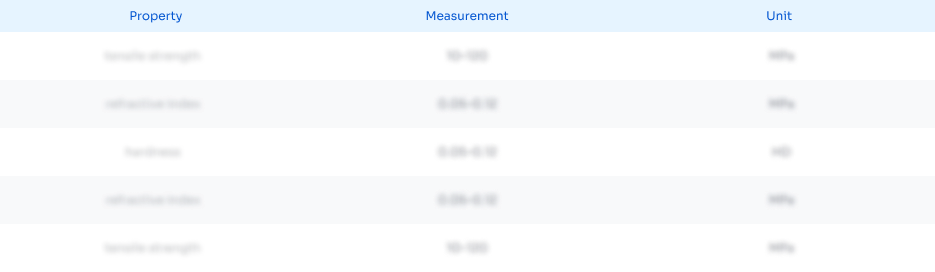
Abstract
Description
Claims
Application Information

- R&D
- Intellectual Property
- Life Sciences
- Materials
- Tech Scout
- Unparalleled Data Quality
- Higher Quality Content
- 60% Fewer Hallucinations
Browse by: Latest US Patents, China's latest patents, Technical Efficacy Thesaurus, Application Domain, Technology Topic, Popular Technical Reports.
© 2025 PatSnap. All rights reserved.Legal|Privacy policy|Modern Slavery Act Transparency Statement|Sitemap|About US| Contact US: help@patsnap.com