Preparation method of stereoscopic low-carbon fur spun wool
A wool worsted and worsted spinning technology, which is applied in the field of textile fabrics, can solve the problems of high fabric finishing temperature, long production process cycle, and long process flow, etc., and achieve high yarn bulkiness, strong three-dimensional effect, and reduced twisting The effect of the number of times
- Summary
- Abstract
- Description
- Claims
- Application Information
AI Technical Summary
Problems solved by technology
Method used
Examples
Embodiment 1
[0028] The three-dimensional fabric is woven from ply yarns and single yarns interlaced. The ply yarns and single yarns are worsted yarns, which are blended with wool and lyocell fibers. The yarn count of the worsted yarns is 2 strands 78 public counts and 1 share of 48 public counts, the blending ratio of the worsted yarn is: 50Wt.% of Baolai fiber Paiste, and 50Wt.% of wool. In the weaving process, 5-6 small coils are designed on the circular machine to assemble together the front (upper layer) horizontally and vertically with the reverse (lower layer) long floating threads to form small patterns. Raise the temperature from 40°C to 100°C at a rate of 2°C / min, and keep warm for 55 minutes. The warp stitch density of the fabric is 245 / 10cm, and the weft stitch density is 220 / 10cm.
[0029] In this example, the worsted yarn blended with wool and Polaroid fiber Paiste is used. After special production of weaving and finishing, the production process is reduced, the cycle is sho...
Embodiment 2
[0031] The three-dimensional fabric is woven from ply yarns and single yarns interlaced. The ply yarns and single yarns are worsted yarns, which are blended with wool and lyocell fibers. The yarn count of the worsted yarns is 2 strands 76 public counts and 1 share of 46 public counts, the blending ratio of the worsted yarn is: 45Wt.% of Baolai fiber Paiste, and 55Wt.% of wool. In the weaving process, 8 coils are designed on the circular knitting machine to form a herringbone shape with a reverse slope on the front side to form a wave shape. In the finishing step, the temperature of the liquid flow washing is raised from 40°C to 110°C at 2°C / min, and the temperature is kept for 65 minutes. The warp stitch density of the fabric is 260 / 10cm, and the weft stitch density is 230 / 10cm.
[0032] In this example, the worsted yarn blended with wool and Polaroid fiber Paiste is used. After special production of weaving and finishing, the production process is reduced, the cycle is shorte...
PUM
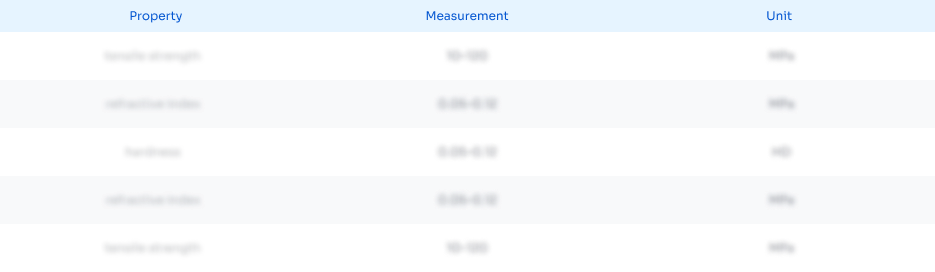
Abstract
Description
Claims
Application Information

- Generate Ideas
- Intellectual Property
- Life Sciences
- Materials
- Tech Scout
- Unparalleled Data Quality
- Higher Quality Content
- 60% Fewer Hallucinations
Browse by: Latest US Patents, China's latest patents, Technical Efficacy Thesaurus, Application Domain, Technology Topic, Popular Technical Reports.
© 2025 PatSnap. All rights reserved.Legal|Privacy policy|Modern Slavery Act Transparency Statement|Sitemap|About US| Contact US: help@patsnap.com