Preparation method for nickel-based superalloy for exhaust valve
A technology of nickel-based high-temperature alloy and exhaust valve, which is applied in the field of alloys, can solve the problems that materials cannot meet the needs, etc., and achieve the effects of reasonable product composition design, good comprehensive performance, and good high-temperature corrosion resistance
- Summary
- Abstract
- Description
- Claims
- Application Information
AI Technical Summary
Problems solved by technology
Method used
Examples
Embodiment 1
[0016] A method for preparing a nickel-based superalloy for an exhaust valve, the alloy is composed of the following components in terms of weight percentage: C 0.10%, Al 4.5%, W 1.5%, Mo 4.0%, Cr 13.5%, V 0.6% , Zr 0.10%, Nb 1.5%, Fe 8.0%, Ta 3.5%, Cu ≤ 0.20, Mn ≤ 0.8, P ≤ 0.020, S ≤ 0.015, Si ≤ 0.3, the balance Ni and unavoidable impurities; the preparation method shown includes The production process of electric furnace smelting, pouring and heat treatment is described as follows:
[0017] (1) Smelting in an intermediate frequency induction furnace according to the above raw material ratio. The smelting temperature is 1600°C. After melting, samples are taken to analyze the composition, and then the composition is adjusted; the nickel-based alloy melted in the intermediate frequency induction furnace is refined with input gas, and the refining temperature is 1640°C. , the refining time is 0.5 hours, to achieve the purpose of degassing, dephosphorization, desulfurization, and...
Embodiment 2
[0021] A method for preparing a nickel-based superalloy for an exhaust valve, the alloy is composed of the following components in terms of weight percentage: C 0.14%, Al 3.5%, W 2.5%, Mo 2.0%, Cr 15.5%, V 0.4% , Zr 0.20%, Nb 0.5%, Fe 12.0%, Ta 2.5%, Cu≤0.20, Mn≤0.8, P≤0.020, S≤0.015, Si≤0.3, the balance of Ni and unavoidable impurities; the preparation method shown includes The production process of electric furnace smelting, pouring and heat treatment is described as follows:
[0022] (1) Smelting in an intermediate frequency induction furnace according to the above raw material ratio. The smelting temperature is 1600°C. After melting, samples are taken to analyze the composition, and then the composition is adjusted; the nickel-based alloy melted in the intermediate frequency induction furnace is refined with input gas, and the refining temperature is 1620°C. , the refining time is 1 hour, to achieve the purpose of degassing, dephosphorization, desulfurization, and blending...
Embodiment 3
[0026] A method for preparing a nickel-based superalloy for an exhaust valve, the alloy is composed of the following components in weight percentage: C 0.12%, Al 4.0%, W 2.0%, Mo 3.0%, Cr 14.5%, V 0.5% , Zr 0.15%, Nb 1.0%, Fe 10.0%, Ta 3.0%, Cu≤0.20, Mn≤0.8, P≤0.020, S≤0.015, Si≤0.3, the balance of Ni and unavoidable impurities; the preparation method shown includes The production process of electric furnace smelting, pouring and heat treatment is described as follows:
[0027] (1) Smelting in an intermediate frequency induction furnace according to the above raw material ratio, the smelting temperature is 1585°C, after melting, take samples to analyze the composition, and then adjust the composition; the nickel-based alloy melted in the intermediate frequency induction furnace is refined with input gas, and the refining temperature is 1630°C , the refining time is 1 hour, to achieve the purpose of degassing, dephosphorization, desulfurization, and blending various trace alloy...
PUM
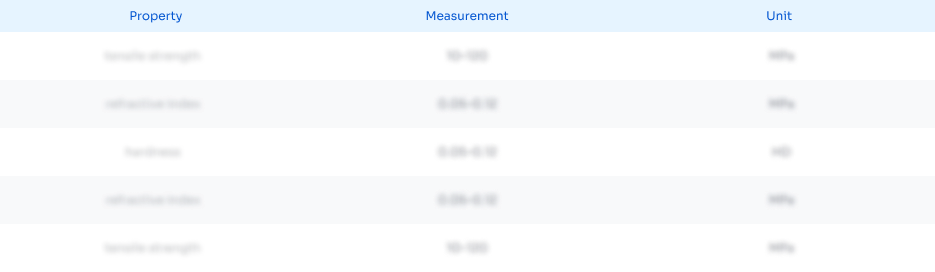
Abstract
Description
Claims
Application Information

- R&D
- Intellectual Property
- Life Sciences
- Materials
- Tech Scout
- Unparalleled Data Quality
- Higher Quality Content
- 60% Fewer Hallucinations
Browse by: Latest US Patents, China's latest patents, Technical Efficacy Thesaurus, Application Domain, Technology Topic, Popular Technical Reports.
© 2025 PatSnap. All rights reserved.Legal|Privacy policy|Modern Slavery Act Transparency Statement|Sitemap|About US| Contact US: help@patsnap.com