Supporting structure of elevator guide rail
A supporting structure and elevator track technology, applied in elevators, transportation and packaging, etc., can solve problems such as cost increase, achieve the effects of reducing track costs, ensuring bending strength, and reducing bending deformation
- Summary
- Abstract
- Description
- Claims
- Application Information
AI Technical Summary
Problems solved by technology
Method used
Image
Examples
Embodiment approach 1
[0038] Next, Embodiment 1 will be described with reference to the drawings.
[0039] figure 1 It is explanatory drawing which shows the rail support structure of Embodiment 1 of this invention, figure 2 is the expanded view of the track support structure, image 3 It is viewed from below (the negative direction of the Z axis) figure 1 Horizontal graph of . in addition, Figure 13 , Figure 14 It is a diagram shown for comparison with the present invention, and is a perspective view of a conventional rail support structure and a horizontal plane internal view viewed from the negative direction of the Z axis.
[0040] Regarding the conventional rail support structure, firstly, the Figure 13 Be explained. The car and the counterweight (not shown) travel up and down along the left and right rails 1 respectively. The rail 1 is supported by the bracket 2 via beams (not shown) provided on the building side. A plurality of brackets 2 are arranged vertically at predetermined...
Embodiment approach 2
[0050] Next, Embodiment 2 will be described with reference to the drawings.
[0051] Figure 4 An example of the rail support structure of Embodiment 2 is shown. In the figure, the shape of the steel plate forming track 10 is the same as figure 1 Differently, it is formed into a shape in which a surface folded back in the X-axis direction of the steel plate forming rail is added to the rail flange end (the outer peripheral end portion opposite to the shape center portion of the rail flange portion) (hereinafter, the folded surface The part is called the reentry part). Rail clamp 3 in figure 1 Set in the YZ plane, in contrast, in Figure 4 Set in the XZ plane.
[0052] Next, use Figure 5 The structure of the bracket 2 will be described. The bracket 2 is composed of a pair of channel-shaped members, which are Figure 17 The steel plate shown is bent into a channel shape. The said turn-back part provided at the rail flange end of the steel plate forming rail 10 and the ...
Embodiment approach 3
[0056] Next, Embodiment 3 will be described with reference to the drawings.
[0057] Figure 7 The rail support structure of this embodiment is shown. The shape and Figure 4 Differently, the turning part turns back 90 degrees at the rail flange end to the opposite side of the rail head (part G indicated by the oblique line in the figure). Rail clamp 3 with Figure 4 Also set in the XZ plane.
[0058] Next, use Figure 8 The structure of the bracket 2 will be described. and Figure 5 Similarly, the bracket 2 is composed of a pair of groove-shaped members, and the folded portion provided at the flange end of the steel plate forming rail 10 is in surface contact with the bottom surface of the groove of the bracket 2 .
[0059] also, Figure 9 Indicates details of fastened parts. The rail pressing plate 3 is fastened to the groove bottom of the bracket 2 by bolts 4 , and the folded portion of the flange end of the steel plate forming rail 10 is fixed by the rail pressing...
PUM
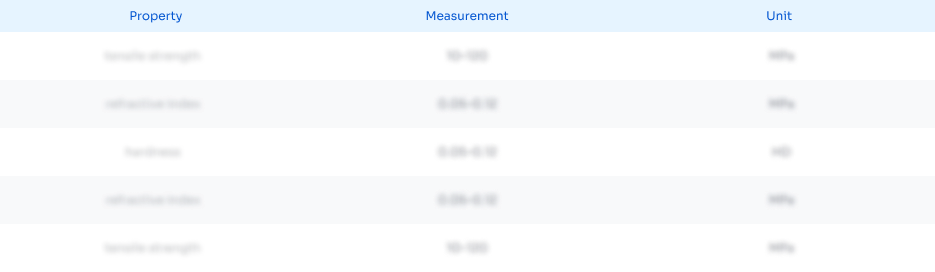
Abstract
Description
Claims
Application Information

- Generate Ideas
- Intellectual Property
- Life Sciences
- Materials
- Tech Scout
- Unparalleled Data Quality
- Higher Quality Content
- 60% Fewer Hallucinations
Browse by: Latest US Patents, China's latest patents, Technical Efficacy Thesaurus, Application Domain, Technology Topic, Popular Technical Reports.
© 2025 PatSnap. All rights reserved.Legal|Privacy policy|Modern Slavery Act Transparency Statement|Sitemap|About US| Contact US: help@patsnap.com