Pattern fixing rack for casting and molding
A fixed frame and pattern technology, which is applied in casting and molding equipment, mold boxes, manufacturing tools, etc., can solve the problems of increasing the cost of molding tooling, reducing production efficiency, affecting the size of casting molds, etc., to save costs, reduce production efficiency, The effect of improving production efficiency
- Summary
- Abstract
- Description
- Claims
- Application Information
AI Technical Summary
Problems solved by technology
Method used
Image
Examples
Embodiment Construction
[0014] A pattern holder for casting moulding, such as figure 1 As shown: it includes a square cushion block 3 with one end high and the other end low. The lower end of the square cushion block 3 is matched with a main body bracket 1 through a fastening pin 2 connected with the pattern 7.
[0015] Such as figure 2 As shown: the main body bracket 1 is assembled by a base 4 that is matched with the lower end of the square block 3 and has the same shape, an upper square top 5 and a rod 6 connecting the two.
[0016] The square block 3 is a rectangular parallelepiped.
PUM
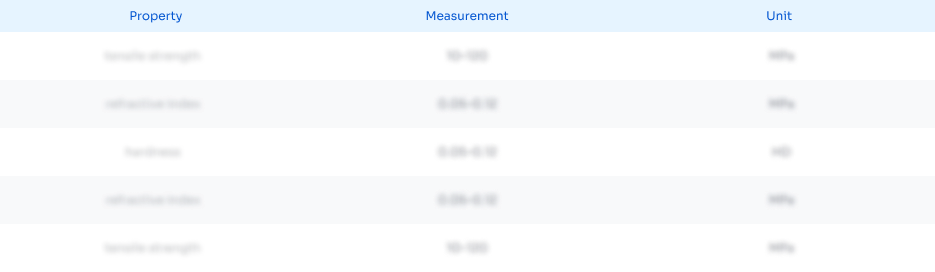
Abstract
Description
Claims
Application Information

- R&D
- Intellectual Property
- Life Sciences
- Materials
- Tech Scout
- Unparalleled Data Quality
- Higher Quality Content
- 60% Fewer Hallucinations
Browse by: Latest US Patents, China's latest patents, Technical Efficacy Thesaurus, Application Domain, Technology Topic, Popular Technical Reports.
© 2025 PatSnap. All rights reserved.Legal|Privacy policy|Modern Slavery Act Transparency Statement|Sitemap|About US| Contact US: help@patsnap.com