Wearable heavy material handling power-assisting bionic exoskeleton
An exoskeleton and wearable technology, applied in medical science, prosthesis, etc., can solve the problems of lack of operational flexibility, high requirements of the working environment, and low efficiency, so as to improve the handling strength and flexibility, and meet the requirements of high-power , Improve the effect of handling efficiency
- Summary
- Abstract
- Description
- Claims
- Application Information
AI Technical Summary
Problems solved by technology
Method used
Image
Examples
Embodiment Construction
[0015] Further illustrate the present invention below in conjunction with accompanying drawing.
[0016] refer to figure 1 , 2 , the wearable bionic exoskeleton for heavy material handling includes upper extremity exoskeleton 21, lower extremity exoskeleton 22 and upper and lower extremity exoskeleton connecting plate 41, etc.; connected in series.
[0017] The connection relationship between each part is as follows:
[0018] Upper limb exoskeleton 21 includes motor drive system box 11, shoulder joint 12, upper arm bar 13, elbow joint 14, forearm bar 15, wrist joint 16, hand mechanism 17, etc.; motor drive system box 11 and upper and lower extremity exoskeleton connecting plates 41 is tightly connected, the motor drive system box 11, the shoulder joint 12, the upper arm bar 13, the elbow joint 14, the forearm bar 15, the wrist joint 16 and the hand mechanism 17 are sequentially connected in series; The rod 15 is flexibly connected to the forearm 62 of the human body, and t...
PUM
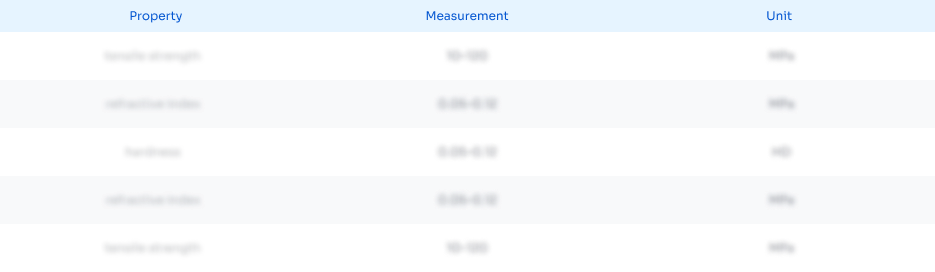
Abstract
Description
Claims
Application Information

- R&D
- Intellectual Property
- Life Sciences
- Materials
- Tech Scout
- Unparalleled Data Quality
- Higher Quality Content
- 60% Fewer Hallucinations
Browse by: Latest US Patents, China's latest patents, Technical Efficacy Thesaurus, Application Domain, Technology Topic, Popular Technical Reports.
© 2025 PatSnap. All rights reserved.Legal|Privacy policy|Modern Slavery Act Transparency Statement|Sitemap|About US| Contact US: help@patsnap.com