Piezoresistive micromechanical sensor component and corresponding measuring method
A technology of micro-mechanical sensor and measurement method, which is applied in the direction of measuring device, acceleration measurement, speed/acceleration/shock measurement, etc., can solve the problems of process consumption, etc., and achieve the effect of favorable cost, high mechanical sensitivity, and simplified technical realization
- Summary
- Abstract
- Description
- Claims
- Application Information
AI Technical Summary
Problems solved by technology
Method used
Image
Examples
Embodiment Construction
[0025] In the figures, identical reference numbers designate identical or functionally identical components.
[0026] figure 1 is a top view of a piezoresistive micromechanical sensor device in the form of a micromechanical acceleration sensor device according to a first embodiment of the invention, and Figure 2a -c is based on figure 1 A cross-section along lines AA1', BB' and CC' of a piezoresistive micromechanical sensor device in the form of a micromachined acceleration sensor device.
[0027] exist figure 1 , reference numeral 5 shows a piezoresistive micromachined acceleration sensor. Starting from the substrate 1, two uniformly doped piezoresistive beams 1a, 1b extend to the anti-seismic mass 3, whereby the anti-seismic mass is connected to the substrate 1 via the beams 1a, 1b. There is a cavity K below the beams 1 a , 1 b and the seismic mass 3 .
[0028] The insulating trench G between the piezoresistive beams 1 a , 1 b can also be embodied as a narrow insula...
PUM
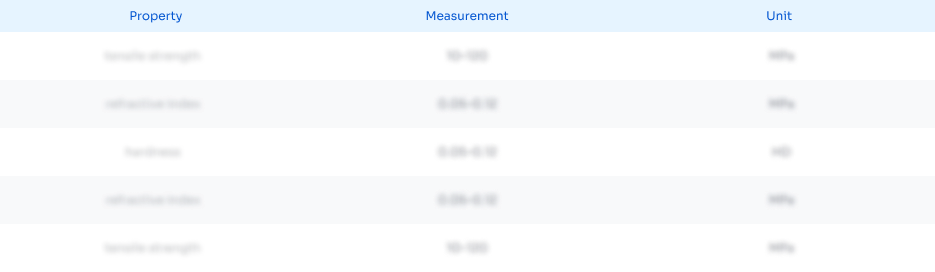
Abstract
Description
Claims
Application Information

- Generate Ideas
- Intellectual Property
- Life Sciences
- Materials
- Tech Scout
- Unparalleled Data Quality
- Higher Quality Content
- 60% Fewer Hallucinations
Browse by: Latest US Patents, China's latest patents, Technical Efficacy Thesaurus, Application Domain, Technology Topic, Popular Technical Reports.
© 2025 PatSnap. All rights reserved.Legal|Privacy policy|Modern Slavery Act Transparency Statement|Sitemap|About US| Contact US: help@patsnap.com