Prefabricated framework infilled wall
A technology for filling walls and skeletons, applied to walls, building components, buildings, etc., can solve the problems of low strength of filling walls, high cost of main structure, complicated construction technology, etc., and achieve fast wall formation, low overall cost, and on-site construction The effect of simple process
- Summary
- Abstract
- Description
- Claims
- Application Information
AI Technical Summary
Problems solved by technology
Method used
Image
Examples
Embodiment 1
[0027] like Figure 13 The circular arc waveform prefabricated skeleton 1 (vertical length 2900, width 1000 including 5 waves, arch height 60, wall thickness 20) is delivered to the construction site after being prefabricated in the factory, and filled in the wall according to the middle distance of 1050 and the gap width of 50 The buckle arrangement in the axial plane is fixed on the upper and lower floors with expansion bolts. The corrugated metal tire net 6 (thickness 30, wave width 50) is prefabricated in the factory and delivered to the construction site. Vertical to the height direction of the skeleton 1, the pipeline is laid in the cavity in two directions, the cement sand is dry-mixed according to the ratio of 1:2, and then packed and transported to the construction site. 20 thick on the rib 4 and the tire net 6, after reaching a certain strength, the surface layer 2 is now smeared with 15 thick vitrified microbead thermal insulation mortar, and the surface is scraped ...
Embodiment 2
[0029] like Figure 14 The L-shaped prefabricated skeleton 1 shown (vertical length 2900, long leg 1000, short leg 100, wall thickness 20) is delivered to the construction site after prefabricated in the factory, and every two anti-symmetric buckles are combined, according to the middle distance 1050 and the gap width 50 are arranged in the central axis plane of the filling wall and fixed on the upper and lower floors with expansion bolts, the pipeline is laid in the vertical rib 4 and the surface layer 2, and the cement sand is dry-mixed according to the ratio of 1:2 and then packed in bags and delivered to construction On site, apply or spray on the outer side of the vertical rib 4 and the wall at a thickness of 20 thick, and the prepared desulfurized gypsum that has been retarded for 30 minutes is transported to the construction site, add water and mix well, and then apply or spray on the inner side of the wall at a thickness of 20 After reaching a certain strength, the sur...
Embodiment 3
[0031] like Figure 15 The W-shaped prefabricated frame 1 shown (vertical length 2900, width 1000, arch height 60, wall thickness 20) is delivered to the construction site after being prefabricated in the factory. The front and back are arranged staggeredly and fixed on the upper and lower floors with expansion bolts. The retarded phosphogypsum is transported to the construction site. After adding water and stirring well, it is now painted or sprayed on both sides of the prefabricated skeleton 1. The total thickness is 90. After reaching a certain strength, the surface Just scrape the putty. This example is for an interior partition wall.
PUM
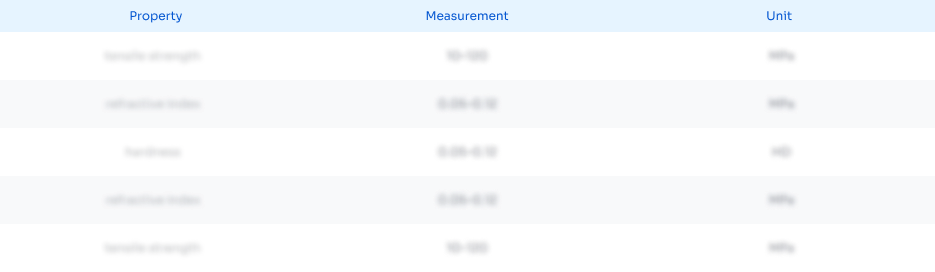
Abstract
Description
Claims
Application Information

- R&D Engineer
- R&D Manager
- IP Professional
- Industry Leading Data Capabilities
- Powerful AI technology
- Patent DNA Extraction
Browse by: Latest US Patents, China's latest patents, Technical Efficacy Thesaurus, Application Domain, Technology Topic, Popular Technical Reports.
© 2024 PatSnap. All rights reserved.Legal|Privacy policy|Modern Slavery Act Transparency Statement|Sitemap|About US| Contact US: help@patsnap.com